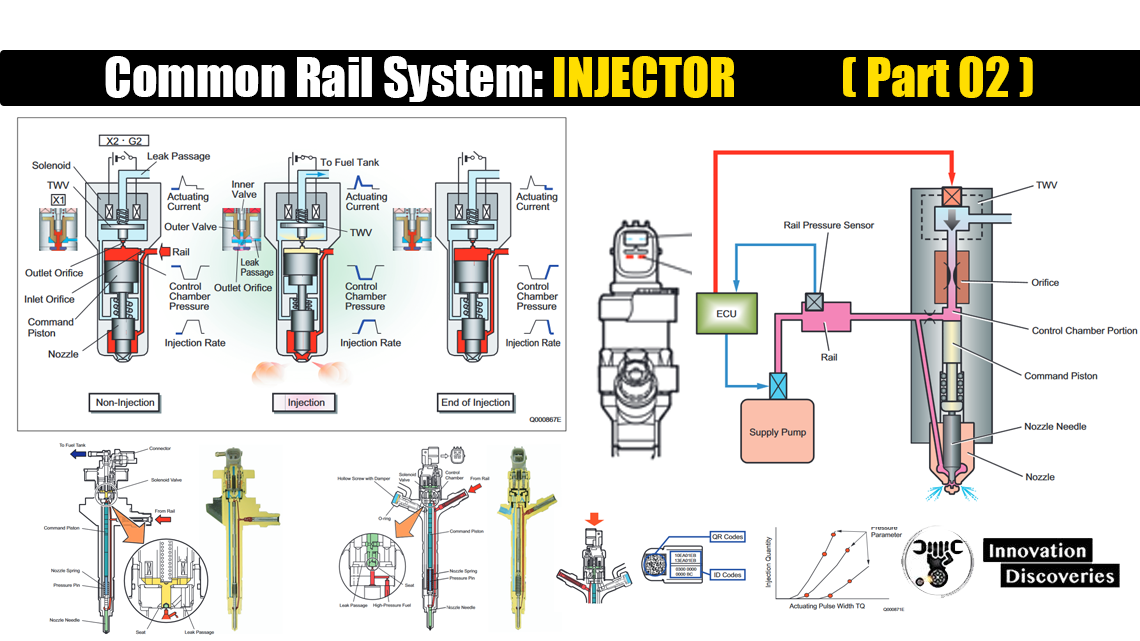
Introduction
The fuel injection system is a crucial component of modern internal combustion engines, responsible for delivering the correct amount of pressurized fuel into the combustion chamber at precise timings and rates.
This process significantly influences engine performance, fuel efficiency, and emission levels. At the heart of this system are the fuel injectors, which are controlled by signals from the Engine Control Unit (ECU).
This document explores the construction, types, and operation of these injectors, emphasizing their role in achieving optimal engine performance and efficiency.
- The injector injects the pressurized fuel in the rail into the engine combustion chamber at the optimal injection timing, injection quantity, injection rate, and injection pattern, in accordance with signals from the ECU.
- Injection is controlled using a TWV (Two-Way Valve) and orifice. The TWV controls the pressure in the control chamber to control the start and end of injection. The orifice controls the injection rate by restraining the speed at which the nozzle opens.
- The command piston opens and closes the valve by transmitting the control chamber pressure to the nozzle needle. When the nozzle needle valve is open, the nozzle atomizes the fuel and injects it.
- There are three types of injectors: the X1, X2, and G2.
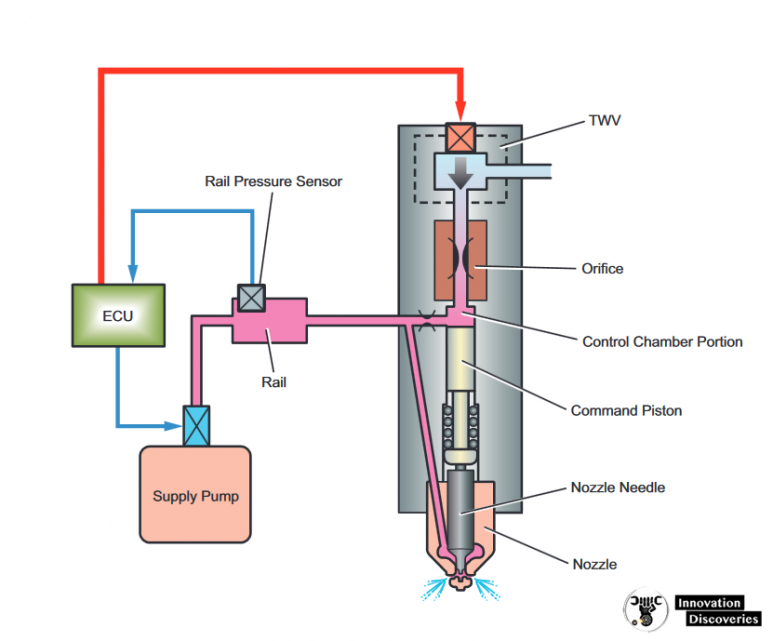
Injector Construction and Features
The injector consists of a nozzle similar to the conventional “nozzle & nozzle holder”, an orifice that controls the injection rate, the command piston, and a TWV (two-way solenoid valve).
The basic construction is the same for the X1, X2, and G2 types.
(1) X1 Type
- Precision control is attained through electronic control of the injection. The TWV comprises two valves: the inner valve (fixed) and the outer valve (movable).
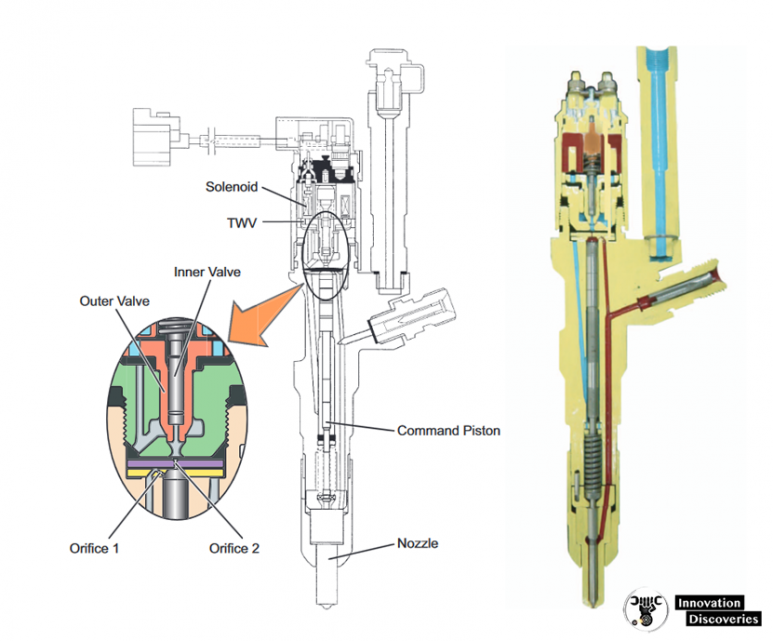
(2) X2 Type
- By reducing the injector actuation load, the injector has been made more compact and energy efficient, and its injection precision has been improved. The TWV directly opens and closes the outlet orifice.
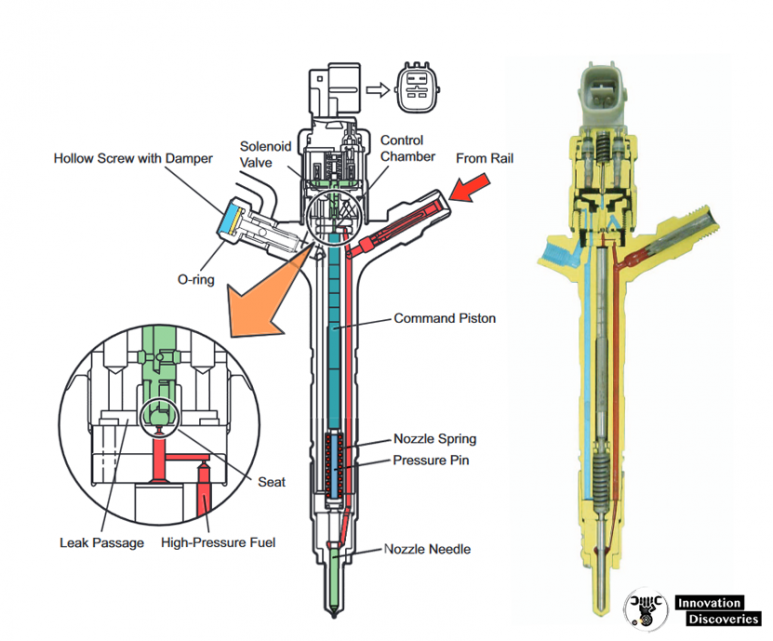
(3) G2 Type
- To ensure high pressure, the G2 type has improved pressure strength, sealing performance and pressure wear resistance. It also has improved high-speed operability, enabling higher-precision injection control and multi-injection.
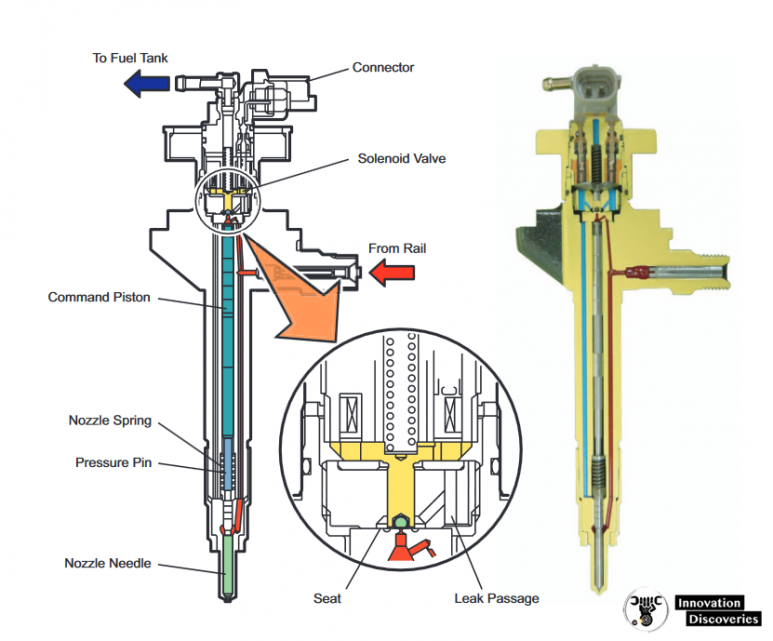
NOTE : Multi-injection means that for the purpose of reducing exhaust gas emissions and noise, the main injection is accomplished with one to five injections of fuel without changing the injection quantity.
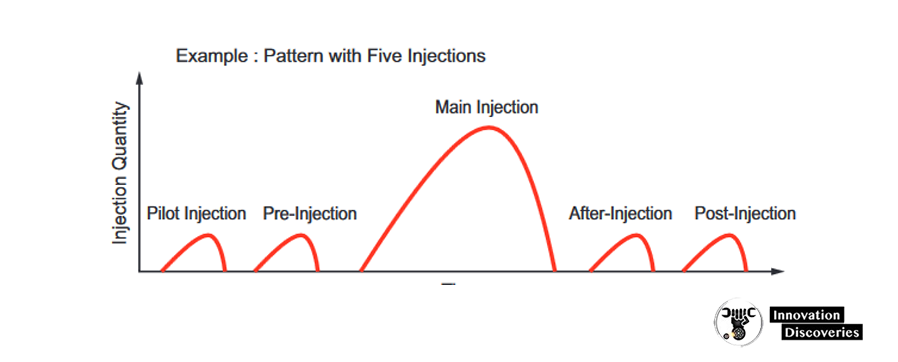
Injector Operation
The injector controls injection through the fuel pressure in the control chamber. The TWV executes leak control of the fuel in the control chamber to control the fuel pressure within the control chamber. The TWV varies with the injector type.
Non-Injection
When the TWV is not energized, the TWV shuts off the leak passage from the control chamber, so the fuel pressure in the control chamber and the fuel pressure applied to the nozzle needle are both the same rail pressure.
The nozzle needle thus closes due to the difference between the pressure-bearing surface area of the command piston and the force of the nozzle spring, and fuel is not injected.
For the X1 type, the leak passage from the control chamber is shut off by the outer valve being pressed against the seat by the force of the spring, and the fuel pressure within the outer valve. For the X2/G2 types, the control chamber outlet orifice is closed directly by the force of the spring.
Injection
When TWV energization starts, the TWV valve is pulled up, opening the leak passage from the control chamber.
When this leak passage opens, the fuel in the control chamber leaks out and the pressure drops. Because of the drop in pressure within the control chamber, the pressure on the nozzle needle overcomes the force pressing down, the nozzle needle is pushed up, and injection starts. When fuel leaks from the control chamber, the flow quantity is restricted by the orifice, so the nozzle opens gradually.
The injection rate rises as the nozzle opens. As current continues to be applied to the TWV, the nozzle needle eventually reaches the maximum amount of lift, which results in the maximum injection rate. Excess fuel is returned to the fuel tank through the path shown.
End of Injection
When TWV energization ends, the valve descends, closing the leak passage from the control chamber. When the leak passage closes, the fuel pressure within the control chamber instantly returns to the rail pressure, the nozzle closes suddenly, and injection stops.
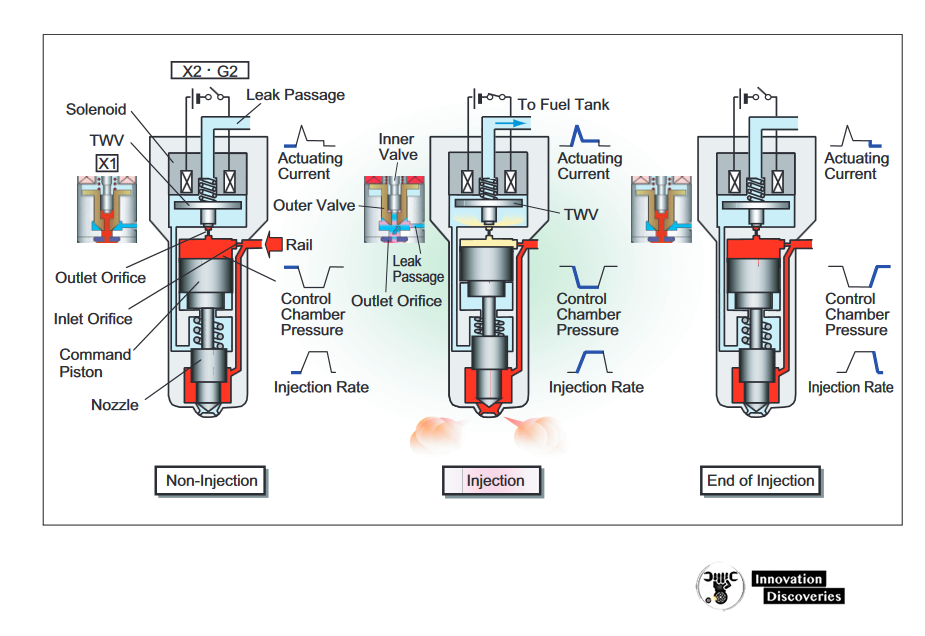
Injector Actuation Circuit
In order to improve injector responsiveness, the actuation voltage has been changed to high voltage, speeding up both solenoid magnetization and the response of the TWV.
The EDU or the charge circuit in the ECU raises the respective battery voltage to approximately 110V, which is supplied to the injector by signal from the ECU to actuate the injector.
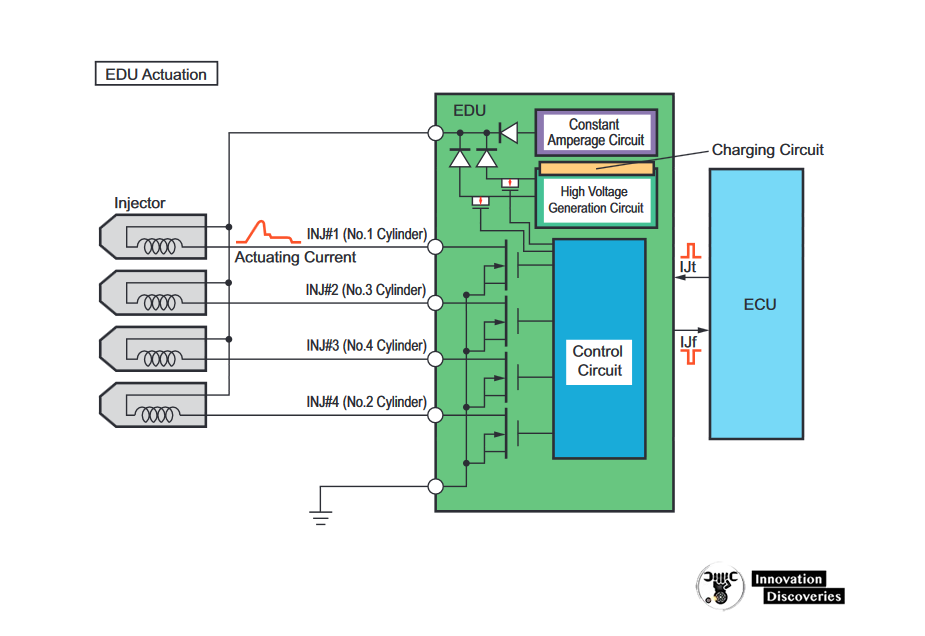
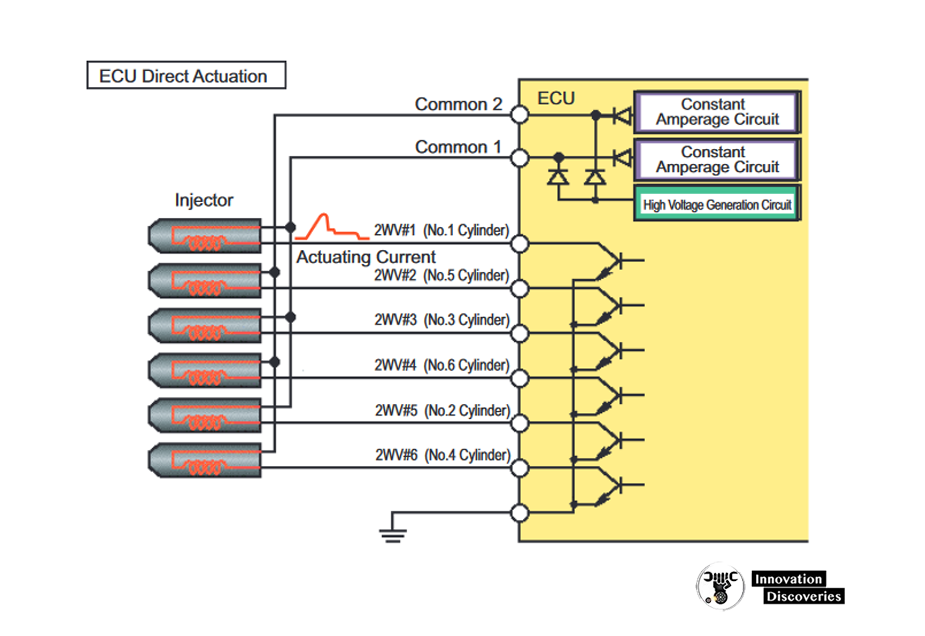
Other Injector Component Parts
(1) Hollow Screw with Damper
- The hollow screw with damper enhances injection quantity accuracy, by reducing the back-pressure pulsations (pressure fluctuations) of the leak fuel.
In addition, it minimizes the back-pressure dependence (the effect of the pressure in the leak pipe changing the injection quantity even though the injection command is the same) of the fuel in the leak
pipe.
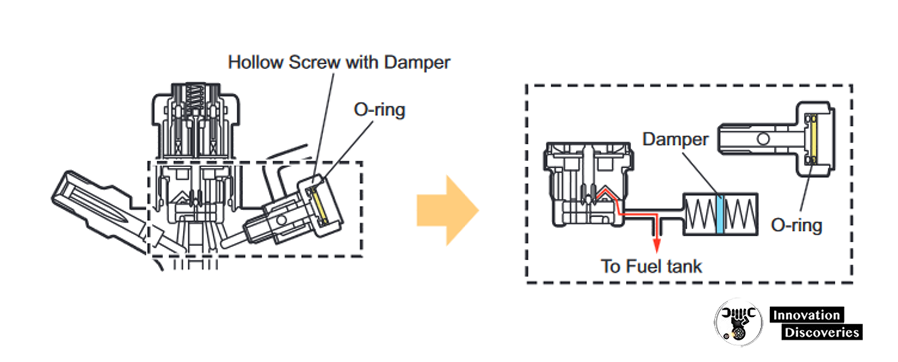
(2) Connector with Correction Resistor
- The connector with correction resistor has a built-in correction resistor in the connector section to minimize injection quantity variation among the cylinders.
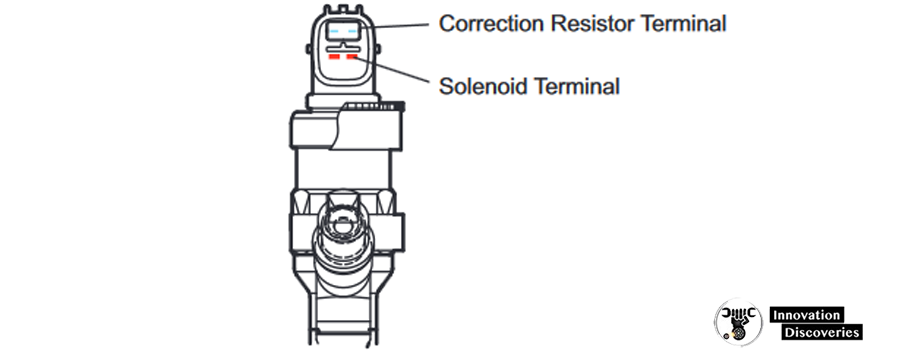
(3) Injector with QR Codes
- QR (Quick Response) codes have been adopted to enhance correction precision. The QR code, which contains the correction data of the injector, is written to the engine ECU.
QR codes have resulted in a substantial increase in the number of fuel injection quantity correction points, greatly improving injection quantity precision.
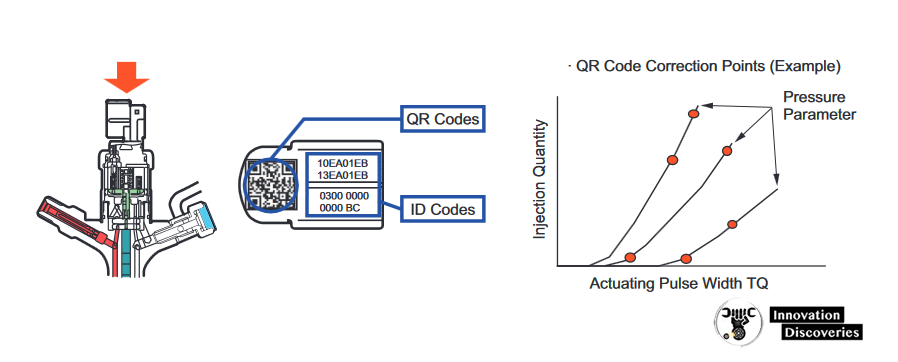
NOTE : QR codes are a new two-dimensional code that was developed by DENSO. In addition to injection quantity correction data, the code contains the part number and the product number, which can be read at extremely high speeds.
Handling Injectors with QR Codes (Reference)
- Injectors with QR codes have the engine ECU recognize and correct the injectors, so when an injector or the engine ECU is replaced, it is necessary to register the injector’s ID code in the engine ECU.
Replacing the Injector
- It is necessary to register the ID code of the injector that has been replaced in the engine ECU.
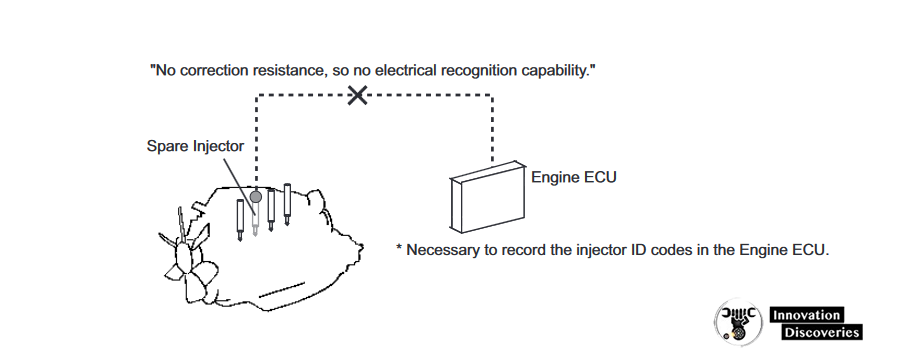
Replacing the Engine ECU
- It is necessary to register the ID codes of all the vehicle injectors in the engine ECU.
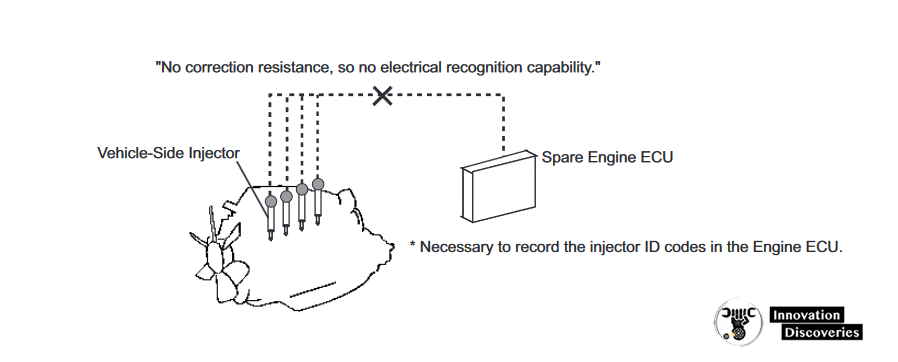
Injector Overview
Injectors are designed to deliver pressurized fuel from the rail into the engine’s combustion chamber, with timing, quantity, rate, and pattern dictated by the ECU.
They achieve this through a sophisticated mechanism involving a Two-Way Valve (TWV), orifices, and command pistons.
The operation of injectors is characterized by their ability to start and stop fuel injection quickly and precisely, contributing to the engine’s overall efficiency and emission control.
Injectors are categorized into three types—X1, X2, and G2—each with unique features and advantages.
The X1 type focuses on electronic control for precision, the X2 type offers compactness and energy efficiency, while the G2 type is designed for high-pressure applications with multi-injection capabilities.
These types share a common structure but differ in their specific control mechanisms.
Conclusion
Fuel injectors play a pivotal role in the operation of modern engines, ensuring efficient fuel delivery, reducing emissions, and contributing to overall engine performance.
The use of TWVs, orifices, and advanced control systems allows for precise fuel injection, which can be adjusted based on engine requirements and driving conditions.
Additionally, the integration of QR codes in injectors adds a layer of precision to the correction process, enhancing the accuracy of fuel delivery.
Understanding the different types of injectors and their operation provides valuable insights into engine maintenance and performance optimization.
Proper handling of injectors with QR codes, including correct registration during replacement or maintenance, is essential for maintaining engine efficiency and compliance with emission standards.
By mastering the concepts and details outlined in this guide, one can ensure the proper functioning of a vehicle’s fuel injection system, leading to better engine performance and reduced environmental impact.
Credit goes to : Denso HPCR manual
Part 01
Read More About Common Rail System
Visit Forum
Visit Our Friendly Website
