Lubrication system is used to introduce oil and other lubricants to give a flow to the clean oil at the accurate temperature with an appropriate pressure to moving machine parts.
The oil is sucked out into the pump from the sump thereby reducing the friction between parts and therefore increasing the longevity of all components. Without lubrication, most machines would overheat or suffer extreme damage.
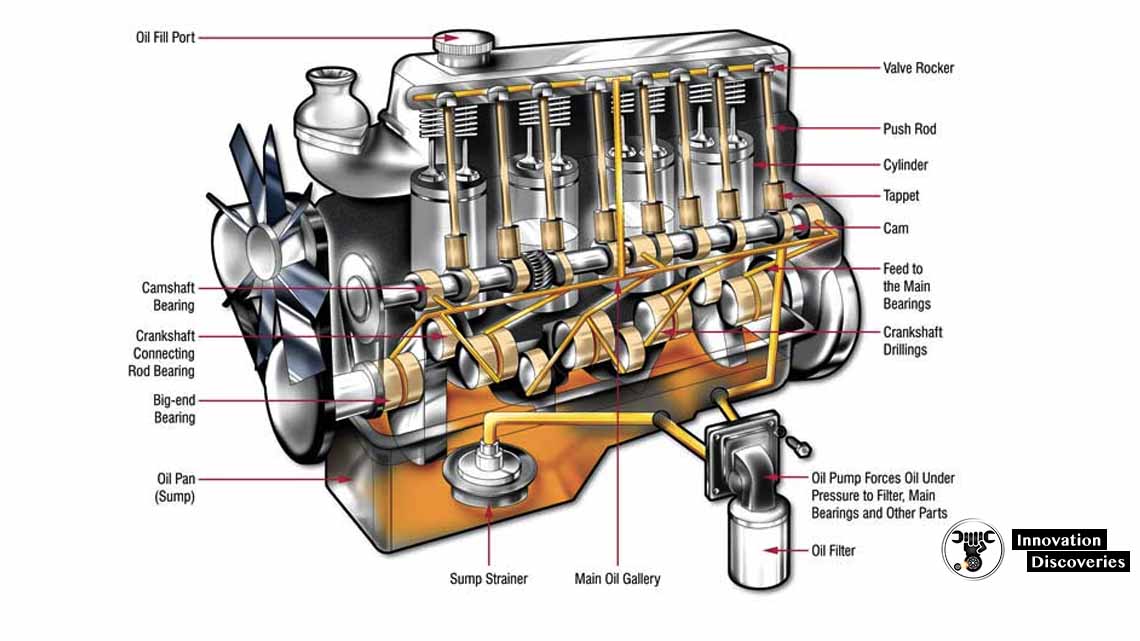
Proper lubrication is the most important aspect of machine and auto life. A well-oiled automobile will outlast poorly maintained models easily.
Industrial machinery is the same and a good lubrication system can help save a lot of money in the long run.
The different types of lubrication systems used are
1. Mist lubrication system
2. Wet sump lubrication system, and
3. Dry sump lubrication system
1. Mist lubrication system
In this system, A small quantity of lubricating oil is mixed with fuel (mostly gasoline). The oil and fuel mixture is introduced through the carburetor. The gasoline is vaporized and oil which is in the form of mist enters the cylinder via the crank base.
The droplets of oil strike the crank base lubricate the main and connecting rod bearings and the rest of the oil lubricates the piston, piston rings and cylinder.
The system is preferred in two-stroke engines where crank base lubrication is not required.
In a two-stroke engine, the charge is partially compressed in a crank base, SO, it is not possible to have the oil in the crank base.
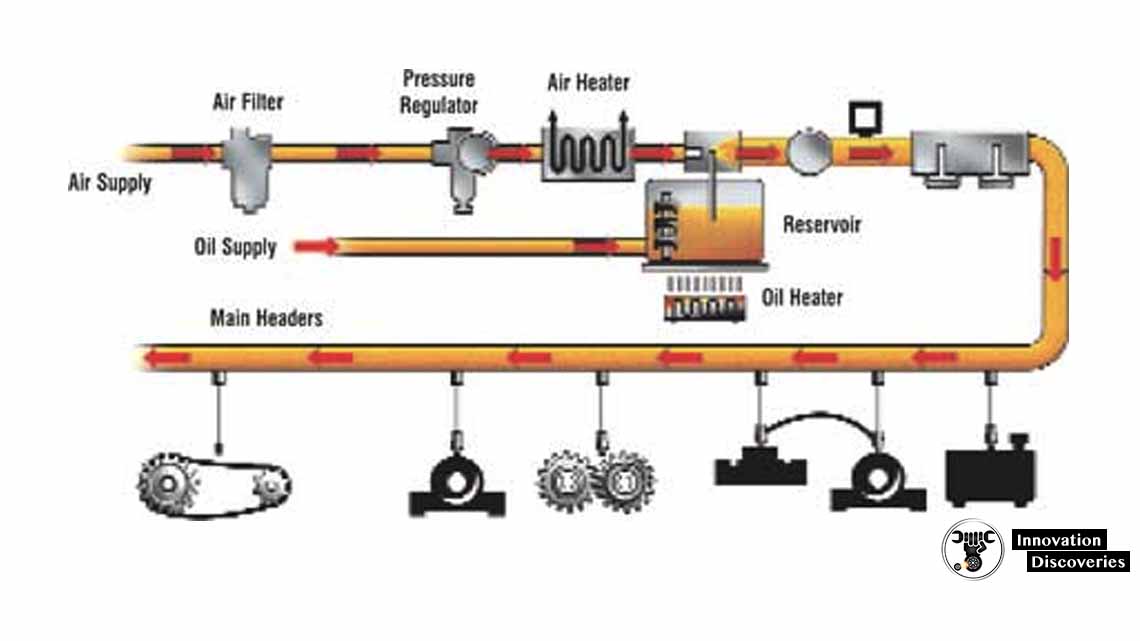
The various advantages are:
- No oil changes and reduced maintenance requirements
- Reduced lubricant consumption (up to 70 percent compared to sump lubrication)
- Lower friction and reduced bearing temperatures
- Mist delivery pressure blocks entrance of contaminants
- Less wear and increased life of machine elements
- Lower capital costs
This system is simple, low cost and maintenance-free, Because it does not require any oil pump, filter, etc.
However, it has certain serious disadvantages.
2. Wet-sump lubrication system
This system consists of a large storing capacity of oil at the base of the crank chamber from the sump, the oil is drawn by the pump and applied to various parts of the engine.
Excess oil after serving the purpose will gradually return to the sump.
There are three varieties in the wet-sump lubrication system. They are:
1. Splash lubrication system
2. Splash and pressure system and
3. Pressurized lubrication system
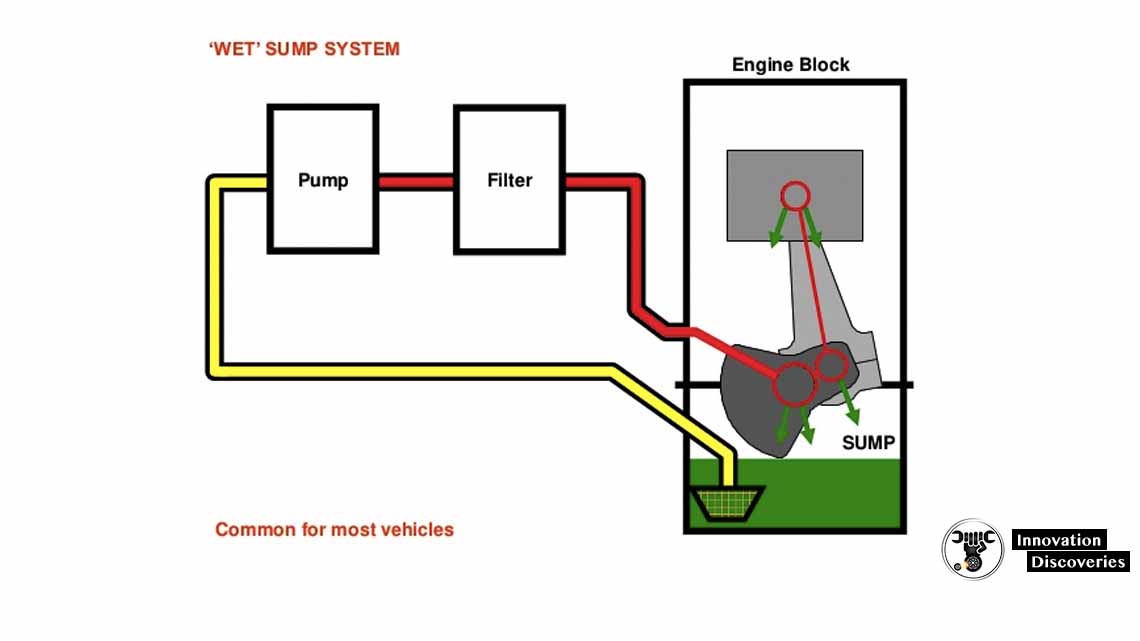
2.1 Splash Lubrication System:
In splash lubrication, oil is applied to the cylinders and pistons by rotating dippers on the connecting-rod bearing caps.
Each time they rotate, the dippers pass through an oil-filled trough. After running through the oil trough the dippers splash oil onto the cylinders and pistons to lubricate them.
While splash lubrication is effective for smaller engines and pumps, it’s not a precise process. Parts of the pump may be insufficiently oiled or oiled too much. The amount of oil in the trough is vital for proper operation.
If there is not enough oil, wear between critical components may occur and too much oil will cause excessive lubrication, which can lead to hydraulic lock. The type of oil used and its viscosity is also important in a splash lube system.
The oil must be thick enough to provide sufficient lubrication and cling to the dippers But not so viscous that it heats up as it is churned about in the oil trough.
Oil purity is also critical oil should be filtered regularly and replenished when necessary.
2.2 Splash and pressure lubrication system:
Splash and pressure lubrication system is a combination of splash and pressure system. In this system, the lubricating oil is supplied by a pump under pressure to main and camshaft bearings.
The oil is also directed in the form of a spray from the nozzle or splashed by scoop or dipper on the big end to lubricate bearings at the big end of the connecting rod, crankpin, gudgeon pin, piston rings, and cylinder.
2.3 Pressurized lubrication system:
In a pressurized lubrication system, the lubricating oil is supplied by a pump under pressure to all parts requiring lubrication. The oil under the pressure is supplied to main bearings of the crankshaft, camshaft and connecting rod bearing surfaces.
Holes drilled through the main crankshaft bearings journals communicate oil to big end bearing and small end bearings through the hole drilled in the connecting rod.
A pressure gauge is provided to confirm the circulation of oil to various parts. The pressure system incorporates a premium spin-on oil filter. Pressure lubrication is used on select single cylinder and connecting rod bearing surfaces.
3. Dry-sump lubrication system:
The dry sump pump is designed with multiple stages, to insure that all the oil is scavenged from the pan. This also results in removing excess air from the crankcase and is the reason they are called “dry sump” meaning the oil pan is essentially dry.
The oil supply is carried from an external tank. Oil from the sump is pumped using a scavenging pump
Through filters to the external storage to the oil from the storage tank is pumped to engine cylinder through an oil cooler.
The oil pressure may vary from 3 to 8 bar. The dry-sump lubrication system is generally used for heavy-duty engines.
When dealing with any lubricating system make sure to service all filters to keep dust out of the lubricant.
Also, regularly change lubricants according to manufacturer recommendations and check your systems daily. Any changes in performance should alert you for potential problems.
Read More: