Metal wire ropes, industrial ropes or cables are the combinations of
Several metallic wires,
Twisted together for extra strength and endurance.
This product is widely used in various heavy-duty industries like mining,
Shipping, transportation, loading/ unloading and even for transmission of electricity.
If recalling the history,
The industrial ropes were invented by a German mining engineer
Wilhelm Albert and used for mining at Harz Mountains Saxony, Germany.
These cables proved to be superior from other ropes and;
Metallic chains in performance and were widely accepted around the world.
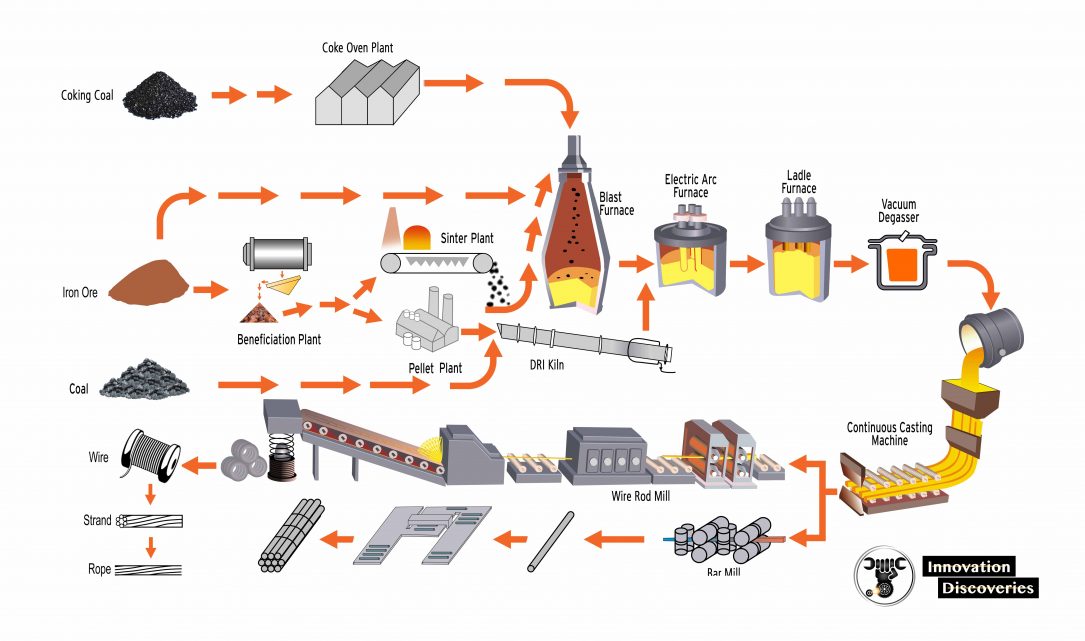
For a layman, the manufacturing process of industrial ropes is the same as that ropes
Made up of natural yarn or synthetic polymer. But in an actual sense, these industrial
Ropes have to undergo a lot of engineering processes. These are wound around a central rope into loops and then laid down into cables. The main ropes are man-made or natural.
Manufacturing Process of Industrial Ropes
The core ropes are made up of natural or man-made fibres;
Which enable firm cushioning to the wires,
Maintain the rope structure and provide internal lubrication.
To know better about the industrial ropes the engineer should have the
Clear understanding of the terminologies like
Rope Diameter, Length, Layout type, and its Dimensions, Tensile Strength,
Type of Core used and Strands.
Also, read – How Boiler Works?
Watch video below
Selection and Quality of Materials
Before manufacturing of the industrial ropes,
It is necessary to decide the dimensions and the core of the cable.
Firstly the raw material is selected for the steel wire,
fibre/core and the lubrication for both wire and core. Determine the Diameter, length, weight and tensile strength of the steel wire.
The Core use of the cable can be made up of natural fibres like Jute,
Manila or Manmade fibres like polyethylene or polypropylene.
Heat Treatment
Annealing is a typical heat treatment given to the steel wires in forming industrial ropes. This process is given to alter the physical and chemical properties of the steel
That enhances its ductility and reduces hardness.
The raw material is heated until the glowing stage
And then slowly cooled down to room temperature. With the help of such heat treatment,
the metal becomes soft and can be prepared for shaping, forming and stamping.
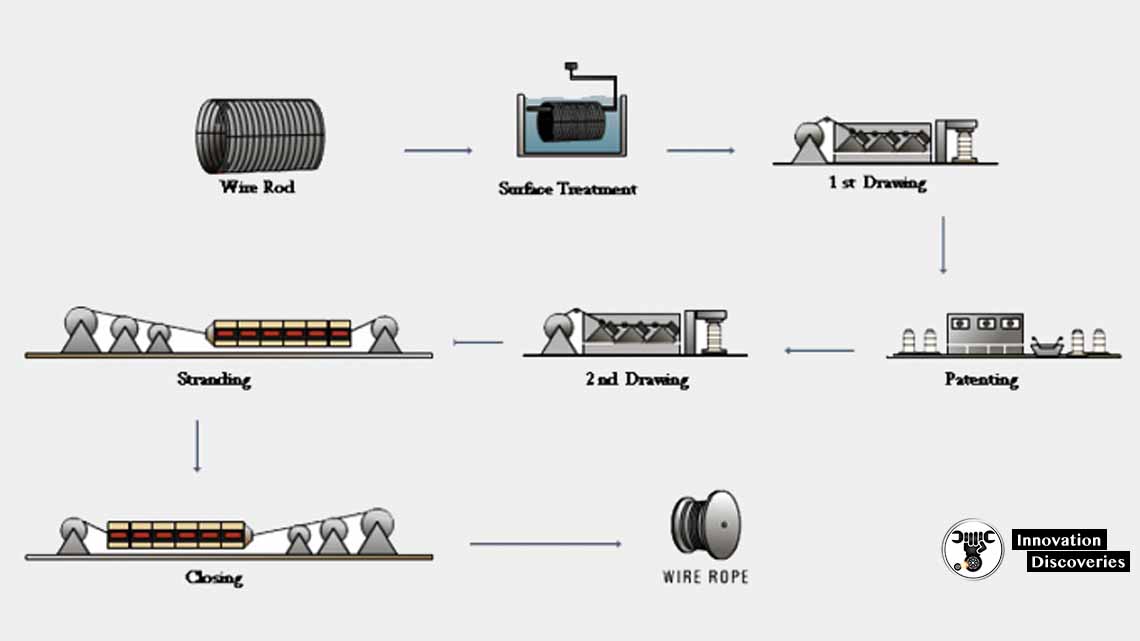
Pickling
Due to heat treatments,
That surface of metal tends to be oxidized, leaving on the surface scales.
The industrial ropes surface treatments are done through the pickling process.
This process helps in removing impurities from the surface like stains,
Rust, and other inorganic contaminants.
Wire Drawing
After the succession of the above treatment processes,
The wire drawing is done. It is a metal forming process which is typically
Used to reduce the cross-section of the wire by pulling the wire in a single or
Multiple strands through drawing dies.
Also, read – Laser Beam Machining
Lubrication
The industrial ropes are galvanized and
Oil impregnation is done for better lubrication. Lubrication helps in reducing friction among the strands and
Helps in the proper movement of the rope over sheaves or spooling on drums. It also helps from corrosion and,
It is recommended to regular lubrication for prolonged use.
Stranding
Standing is combining the steel wires into cables.
This process is very important because through this we are
Able to specify our requirements in the industrial rope formation. The things to be considered here are many wires, strands, and core formation. The stranding speed depends on the feed to the rotating drums.
During this process, the diameter of the cable,
Diameter of the core, type, and direction of lay are specified.
Rope forming
In the industrial rope forming mechanism,
The strands are pulled further through rollers,
And they are rotated to give the shape of the rope and
This feed is further provided to the drums
Which help in pressing and shapinrollers the rope.
Winding/ Closing Operation
At the end of this process,
The industrial rope is properly winded on the spool with any foul and is finished in the required length as specified. The rope end is done by either seizing the rope end or welding it. Sometimes a loop is formed or an attaching is added
At the end as per the industrial requirement.
Factors to choose the right Industrial Rope
Strength:
The strength of the rope mainly depends upon the tensile
Strength of the steel used and the type of construction.
Abrasion resistance:
Ropes with larger outer diameter should be preferred for heavy and better performance.
Flexibility:
With the increase in the number of wires or strands,
The flexibility increases the cable.
Preformed wires:
These wires are very safe,
Easy to use and provide greater resistance to fatigue.
Tensile Strength:
The greater the tensile strength,
The better it works against wear and tear.
Testing
Testing of the industrial wires is done to ensure better industrial performance. The testing includes a tensile test,
Torsion and bending test which help in determining the minimum breaking force of the cable. The dimensioning is done with the help Vernier Callipers and
Measuring tapes to determine the diameter and length of the cable.
Read More: Water Hand Pump: Parts, Types & Working Principle
One Comment