A Rocket Engine is a type of jet engine that uses only stored rocket
Propellant mass for forming its high-speed propulsive jet. Rocket engines are reaction engines obtaining
Thrust by Newton’s third law of motion.
Most rocket engines are internal combustion engines although non-combusting
Forms (such as cold gas thrusters) also exist.
In Rocket Engine, the heat created in the combustion chamber during the combustion process is about 2800K-3500K,
Which contains exhaust gases.
Most of this heat is expelled along with the gas that contains it;
However, heat is transferred to the thrust chamber walls. Due to this high temperature,
There will be an existence of damaging the walls of the thrust chamber and nozzle.
Also, read:
The method of Regenerative Cooling is used to retain such high temperatures effectively.
Regenerative cooling is the most commonly used form of cooling a
The thrust chamber and is achieved by high-velocity Coolant flow over the back of the chamber wall to cool the hot gas liner down. In this method, the fuel itself acts as a coolant, since in liquids A huge amount of heat transfer occurs quickly as comp
The coolant with the heat input from cooling the liner is then discharged
Into the injector and utilized as a propellant.
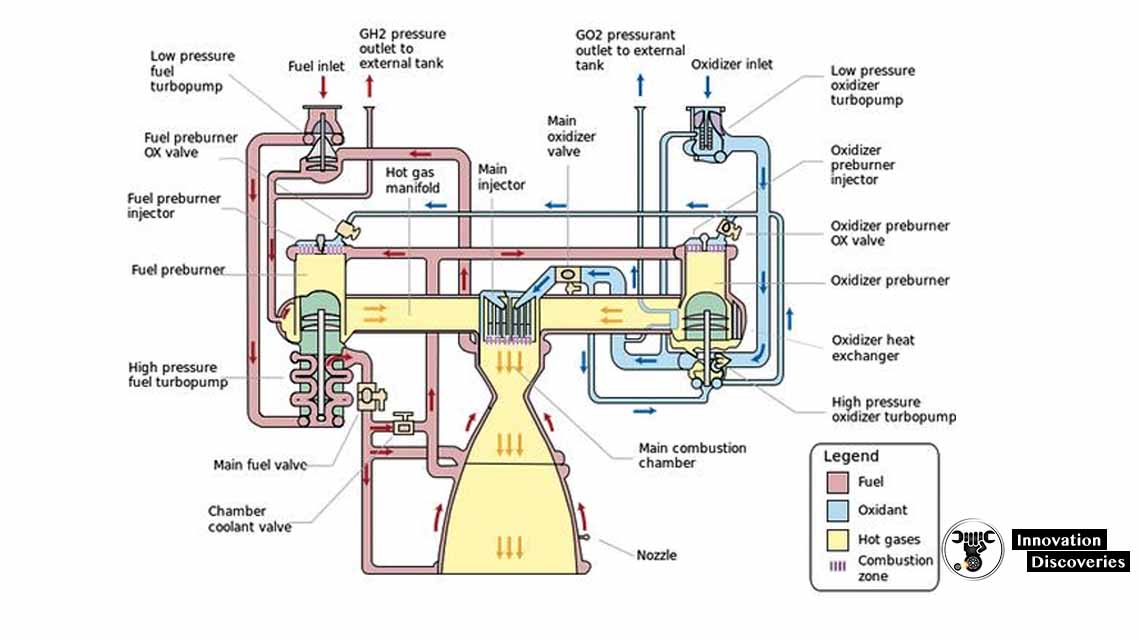
Earlier thrust chamber designs had low chamber pressure,
Low heat flux and low coolant pressure requirements,
Which could be satisfied by a simplified “double-wall chamber”
Design with regenerative and film cooling.
Later, chamber pressures were increased;
And the cooling requirements became more difficult to satisfy.
This led to the design of “tubular wall” thrust chambers,
By far the most widely used design approach for the
Vast majority of large rocket engine applications even in Air Force and NASA. The primary advantage is its lightweight and large experience base. But as chamber pressures and hot gas wall heat fluxes
Continued to increase resulted in more effective methods.
One solution was the “channel wall” thrust chambers, the cooling of the hot gas wall is achieved by flowing the coolant through rectangular channels,
Which are machined into a hot gas liner made from a high-conductivity material,
Such as copper or a copper alloy. Heat transfer and structural characteristics are excellent in this case.
Basically,
There are three domains in a regeneratively cooled rocket engine,
- Gas Domain (Combusted Gases) – Convection and Radiation heat transfer
- Liquid Domain (Coolant) – Convection heat transfer
- Solid Domain (Thrust chamber wall) – Conduction heat transfer
Heat transfer from the outer surface of the thrust chamber to the
Environment can be neglected and the outer
The surface wall is assumed as adiabatic.
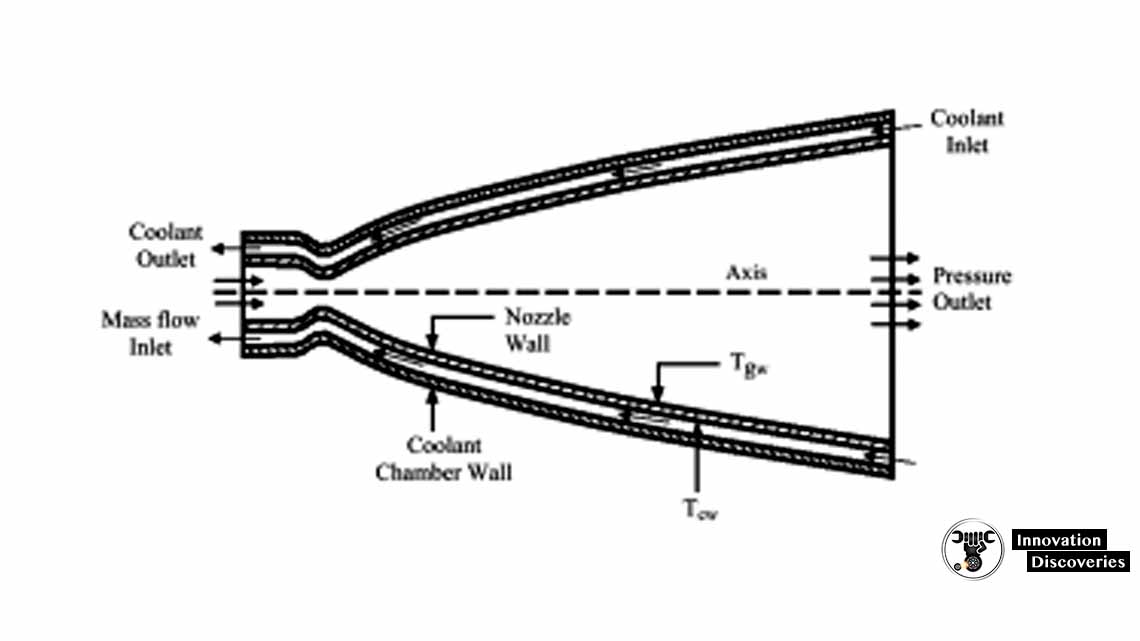
In addition to the regeneratively cooled designs mentioned above,
Other thrust chamber designs have been fabricated for rocket engines using dump
Cooling, film cooling, transpiration cooling,
Ablative liners and radiation cooling.
Although regeneratively cooled combustion chambers have proven to be;
The Best approach for cooling large liquid rocket engines,
Other methods of cooling have also been successfully used for
Cooling thrust chamber assemblies.
Dump cooling, which is similar to regenerative cooling because the coolant flows,
Through small passages over the backside of the thrust chamber wall.
The difference, however, is that after cooling the thrust chamber,
The coolant is discharged overboard through openings at the aft end of the divergent nozzle. This method has limited application because of the performance,
Loss resulting from dumping the coolant overboard.
Film cooling
Protects from excessive heat by introducing a thin film of coolant,
Or propellant through orifices around the injector periphery or manifold orifices
In the chamber wall near the injector or chamber throat region.
This method is typically used in high heat flux regions
And in combination with regenerative cooling.
Transpiration cooling
Provides coolant (either gaseous or liquid propellant)
Through a porous chamber wall at a rate sufficient to maintain the
Chamber hot gas wall to the desired temperature. The technique is a special case of film cooling.
With radiation cooling
The heat is radiated from the outside surface of the combustion chamber or the extension wall of the Nozzle.
Usually, radiation shielding is used in small thrust chambers with,
High-temperature wall material (refractory) and low-heat flux areas,
Such as nozzle extensions.
One Comment