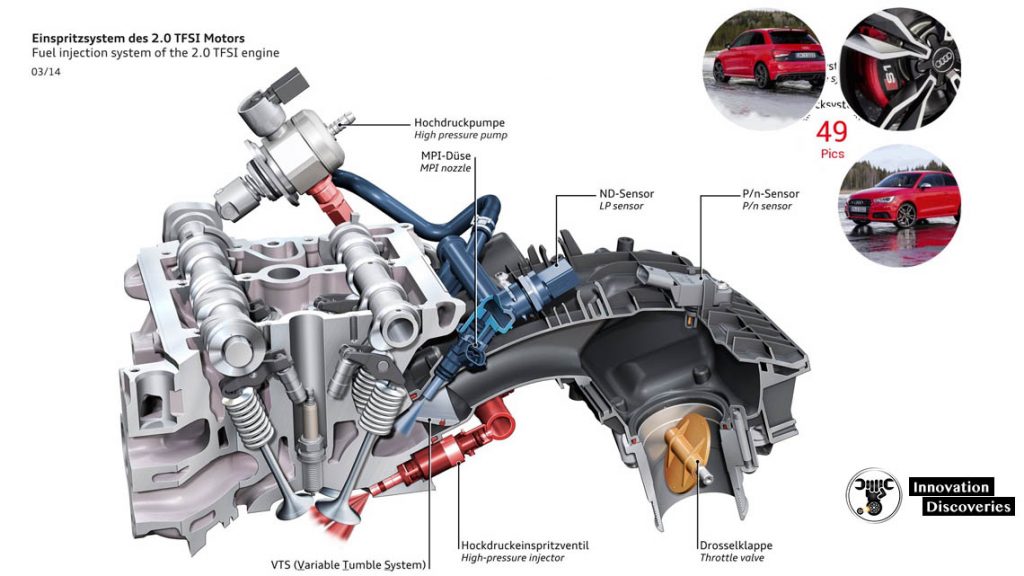
”Fuel injector is an electronically controlled mechanical device
That is responsible for spraying (injecting) the right amount of fuel into the engine
So, that a suitable air/fuel mixture is created for optimal combustion.”
The technology was created in the early 20th century and
Implemented on diesel engines first. By the final third of the 20th century,
It had also become popular among regular gasoline engines.
The electronic control unit (ECU at engine management system)
Determines the precise amount and specific timing of required gasoline
(Petrol) dose for every cycle,
By collecting information from various engine sensors.
So, the ECU sends a command electrical signal of the correct duration and
Timing to the fuel injector coil. In that way opens the injector and allows petrol to
Pass through it into the engine.
The one terminal of the injector coil is directly supplied by
12 volts which are controlled by the ECU,
And the other terminal of the injector coil is open.
When ECU determined the exact amount of fuel and when to inject it,
Activates the appropriate injector by switching the other terminal to the ground
(Mass, i.e. negative pole).
COMPONENTS
The objectives of the fuel injection system are to meter,
Atomize and distribute the fuel throughout the air mass in the cylinder.
At the same time, it must maintain the required air-fuel ratio as
Per the load and speed demand on the engine.
Pumping elements
To move the fuel from the fuel tank to the cylinder.
Metering elements
To measure the supply of the fuel at the rate demanded by speed and load conditioning on the engine
Metering control
To adjust the rate of the metering elements for change in load and speed of the engine.
Mixture control
To adjust the ratio of the fuel and air as demanded by the load and speed.
Distributing elements
To divide the metered fuel equally among the cylinder.
Timing control
To fix the start and stop of the fuel-air mixing process.
TYPES OF FUEL INJECTORS
- Top-Feed – Fuel enters from the top and exits the bottom.
- Side-Feed – Fuel enters on the side on the injector fitting inside the fuel rail.
- Throttle Body Injectors – (TBI) Located directly in the throttle body.
TYPES OF FUEL INJECTION SYSTEMS
1. Single-Point OR Throttle Body Fuel Injection
Also, referred to as a single port,
This was the earliest type of fuel injection to hit the market. All vehicles have an air
Intake manifold where clean air first enters the engine. TBFI works by adding the correct
Amount of fuel to the air before it is distributed to the individual cylinders. The advantage of TBFI is that it’s inexpensive and easy to maintain. If you ever have an issue
With your injector, you’ve only got one to replace.
Additionally, since this injector has a fairly high flow rate,
It’s not as easy to clog up.
Technically, throttle body systems are very robust and require less maintenance. That being said, throttle body injection is rarely used today. The vehicles that still use it are
Old enough that maintenance will be more of an issue than it would with a newer,
Lower mileage car.
Another disadvantage to TBFI is the fact that it’s inaccurate. If you let off the accelerator,
There will still be a lot of fuel in the air mixture that is being sent to your cylinders. This can result in a slight lag before you decelerate or in some vehicles,
It can result in unburned fuel being sent out through the exhaust. This means that TBFI systems are not nearly as fuel-efficient as modern systems.
2. Multiport Injection
Multiport injection simply moved the injectors further down towards the cylinders.
Clean air enters the primary manifold and is directed out towards each cylinder. The injector is located at the end of this port,
Right before it’s sucked through the valve and into your cylinder.
The advantage of this system is that fuel is distributed more accurately,
With each cylinder receiving its spray of fuel. Each injector is smaller and more accurate,
Offering an improvement in fuel economy. The downside is that all injectors spray at the same time,
While the cylinders fire one after the other. This means that you may have leftover fuel in between intake periods,
Or you may have a cylinder fire before the injector has had a chance to deliver additional fuel.
Multiport systems work great when you are traveling at a consistent speed. But when you are quickly accelerating or removing your foot from the throttle,
This design reduces either fuel economy or performance.
3. Sequential Injection
Sequential fuel delivery systems are very similar to multiport systems. That being said, there is one key difference. Sequential fuel delivery is times. Instead of all injectors firing at the same time,
They deliver fuel one after the other.
The timing is matched to your cylinders,
Allowing the engine to mix the fuel right before the valve opens to suck it in. This design allows for improved fuel economy and performance.
Because fuel only remains in the port for a short amount of time,
Sequential injectors tend to last longer and remain cleaner than other systems. Because of these advantages,
Sequential systems are the most common type of fuel injection in vehicles today.
the one small downside to this platform is that it leaves less room for error. The fuel/air mixture is sucked into the cylinder only moments after the injector opens. If it is dirty, clogged, or unresponsive, your engine will be starved of fuel. Injectors need to be kept at their peak performance,
Or your vehicle will start to run rough.
4. Direct Injection
If you’ve started to notice the pattern,
You can probably guess what direct injection is. In this system,
Fuel is squirted right into the cylinder, bypassing the air intake altogether. Premium automobile manufacturers like Audi and BMW would have you believe that
Direct injection is the latest and greatest. About the performance of gasoline vehicles, they’re right! But this technology is far from new. It’s been used in aircraft engines since the second world war,
And diesel vehicles are almost all direct injection
Because the fuel is so much thicker and heavier.
In diesel engines, direct injection is very robust. Fuel delivery can take a lot of abuse,
And maintenance issues are kept to a minimum.
With gasoline engines, direct injection is found almost exclusively in performance vehicles. Because these vehicles operate with very precise parameters, it’s especially
Important to maintain your fuel delivery system. Although the car will continue to run for a long time when neglected,
The performance will quickly decline.
METHODS OF FUEL INJECTION
There are two methods of fuel injection in the compression ignition system
- Airblast injection.
- Airless or solid injection.
Airblast injection
This method was originally used in large stationary and marine engines. But now it is obsolete. In this method, the air is first compressed to very high pressure. A blast of this air is then injected carrying the fuel along with it into the cylinders. The rate of fuel injection is controlled by varying the pressure of the air. The high-pressure air requires a
Multi-stage compressor to keep the air bottles charged. The fuel ignites by the
High temperature of the air caused by high compression. The compressor consumes about 10% of the power developed by the engine,
Decreasing the net output of the engine.
Airless or solid injector
In this method, the fuel under high pressure is directly injected into the combustion chamber. It burns due to the heat of compression of the air. This method requires a fuel
Pump to deliver the fuel at high pressure around 300 kg/cm^2. This method is used for all types of small and big diesel engines. It can be divided into two systems.
- Individual pump system:
In this system, each cylinder has its own individual
High-pressure pump and a measuring unit. - Common rail system: in this system the fuel is pumped by a
Multi-cylinder pump into a common rail,
The pressure in the rail is controlled by a relief valve. A measured quantity of fuel is supplied to each cylinder from the common rail.
This is all about the fuel injection system. If you have any queries regarding this article, ask by commenting. If you like this article, don’t forget to share it on social networks. Subscribe our website for more informative articles. Thanks for reading it.
WORKING PRINCIPLES
The injectors are controlled by the Engine Control Unit (ECU).
First, the ECU obtains information about the engine conditions and
Requirements using different internal sensors.
Once the state and requirements of the engine have been determined,
The fuel is drawn from the fuel tank,
Transported through the fuel lines and then pressurized with fuel pumps. Proper pressure is checked by a fuel pressure regulator. In many cases, the fuel is also divided using a fuel rail to supply the
Different cylinders of the engine. Finally, the injectors are ordered to inject the necessary fuel for the combustion.
The exact fuel/air mixture required depends on the engine,
The fuel used and the current requirements of the engine
(Power, fuel economy, exhaust emission levels, etc.)
5 Comments