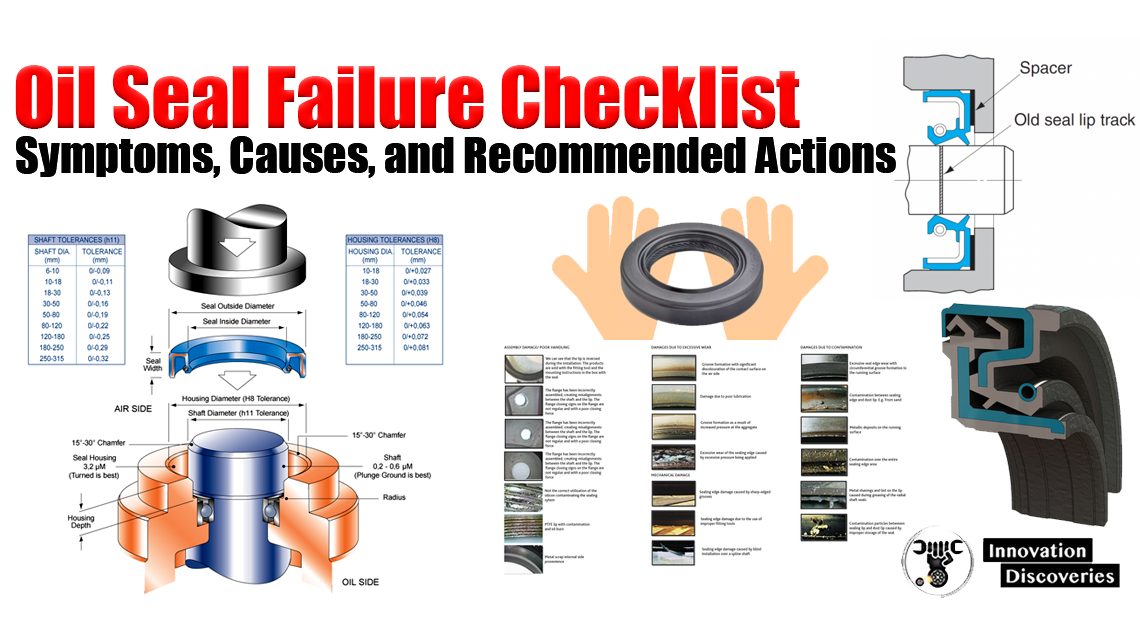
Introduction:
Oil seals, also known as rotary shaft seals, play a crucial role in preventing the leakage of fluids, such as oil, from machinery or equipment. However, there are various factors that can contribute to oil seal failures, leading to leaks and potential damage.
This guide aims to provide an overview of common reasons why oil seals may fail and provides recommendations for addressing these issues.
There are two parts an Oil Seal / Rotary Shaft Seal where leakage can occur:
- The interface between housing bore and seal O.D
- Between the seal lip and shaft
Oil Seal Failure Checklist
SYMPTOM | CAUSE | RECOMMENDED ACTION |
---|---|---|
Oil Seal rotates with shaft | Seal O.D smaller than bore I.D | Select correct size seal and replace |
Oil Seal moves in axial direction along shaft | Seal O.D smaller than bore I.D and caused by the rotating of shaft or the internal pressure | Select correct size seal and replace |
Seal installed in declining condition | The I.D of housing bore is undersized, incorrect means of installation causing the seal to be misaligned | Ensure housing bore is correct size |
Deformation of the metal case | Use of incorrect installation tool | Use correct installation tool |
Damage on the case O.D | The finish of housing is not correct and / or incorrect means of installation Dirt adhering to the seal O.D or the housing I.D | Ensure housing size is correct Use correct installation tool |
Lip worn seriously | Insufficient lubrication Application design restricts lubricant access to seal lip | Ensure sufficient lubricant Change design to ensure seal lip is accessible to lubricant |
Lip worn seriously | Inner pressure too high | Change seal design to pressure type |
Lip partially worn | Seal partially installed T.I.R of I.D and O.D are too big | Select seal with suitable T.I.R (Total Indicated Runout) |
Lip partially worn | Seal misaligned in housing | Ensure housing bore is correct Use correct installation tool |
Lip hardened, worn, and cracked | High temperature, shaft rotation speed, or pressure | Select suitable compound type Supply sufficient lubricant |
Lip material swollen | Incorrect compound selection | Select the correct compound |
Lip scratched | Shaft surface not smooth Scratch caused by incorrect installation tool | Let all the lip configuration clear Install seal correctly |
Lip turning out | Incorrect installation Inner pressure too high | Lubricate the lip and shaft before installation Use pressure type seal |
Crack on the base of flex section | Inner pressure too high Sudden pressure strike on the flex section | Use high-pressure type seals |
Spring dislodged from spring groove | Shaft chamfer is incorrect Incorrect installation The retainer lip is too short | Finish the shaft chamfer and lubricate before installation Be careful while installing Change the seal design |
Conclusion:
Understanding the potential reasons for oil seal failures is essential for maintaining the proper functioning of machinery and preventing leaks. By recognizing the symptoms, identifying the causes, and implementing the recommended actions outlined in the checklist, you can address oil seal issues effectively.
Regular inspection, proper installation techniques, and selecting the correct seal size and compound for the operating conditions are crucial steps in preventing oil seal failures.
Additionally, ensuring sufficient lubrication and addressing issues related to pressure, alignment, and surface conditions can significantly contribute to the longevity and effectiveness of oil seals.
By following this checklist and taking proactive measures, you can minimize the risk of oil seal failures, enhance the performance of your equipment, and avoid potential downtime and costly repairs associated with oil leaks.
Discover More:
Visit Forum
Visit Our Friendly Website
