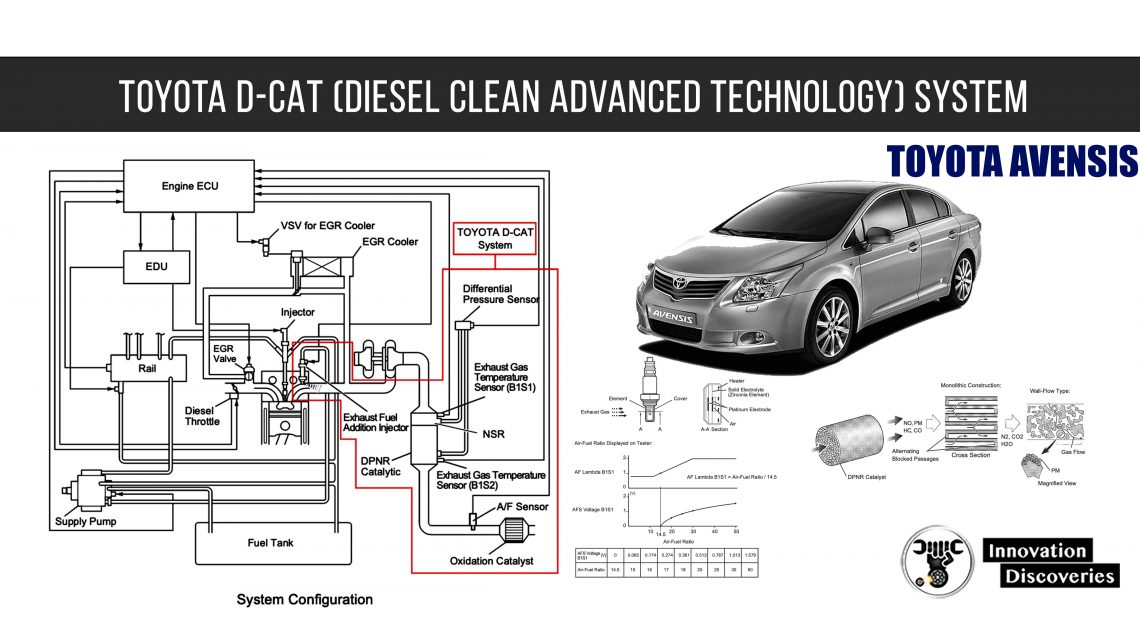
EXHAUST GAS PURIFICATION SYSTEM
Configuration
The exhaust gas purification system for the 2AD-FHV engine consists of the TOYOTA Diesel-Clean Air Technology (D-CAT) system, and the Exhaust Gas Recirculation (EGR) control system.
For the 2AD-FTV, and 1AD-FTV engines (excluding CCO specification vehicles), the exhaust gas purification system consists of the Diesel Particulate Filter (DPF) system, and the EGR control system.
Outline
The TOYOTA D-CAT system used in for the 2AD-FHV engine reduces Particulate Matter (PM), and NOx emissions.
TOYOTA D-CAT comprehensively regulates engine control (consisting of a catalytic system and a fuel injection system) that purifies both particulate matters (PM) and nitrogen oxides (NOx) discharged by diesel engines.
The catalytic system purifies hydrocarbons (HC) and carbon monoxide (CO), and reduces PM and NOx with a catalytic converter with the DPNR system.
The fuel injection system adds fuel into the exhaust port using the exhaust fuel addition injector to produce a rich state for NOx reduction and maintain a proper catalyst temperature for DPNR catalyst regeneration
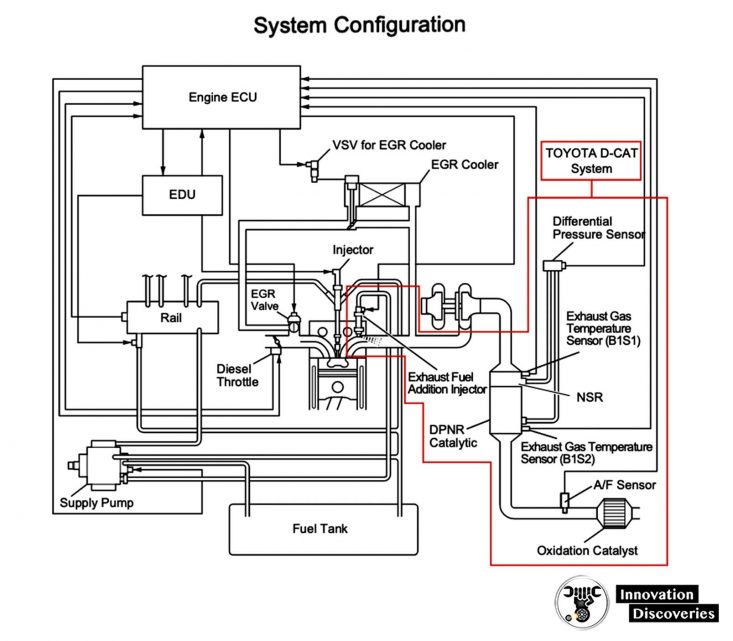
Components
DPNR Catalyst
The DPNR catalyst suppresses drops in exhaust gas pressure and accumulates over 95% of PM by using a porous ceramic filter with high accumulation efficiency, and a low-pressure drop.
In addition, by coating the surface of the filter with a NOx adsorber catalyst, NOx can be reduced through adsorption.
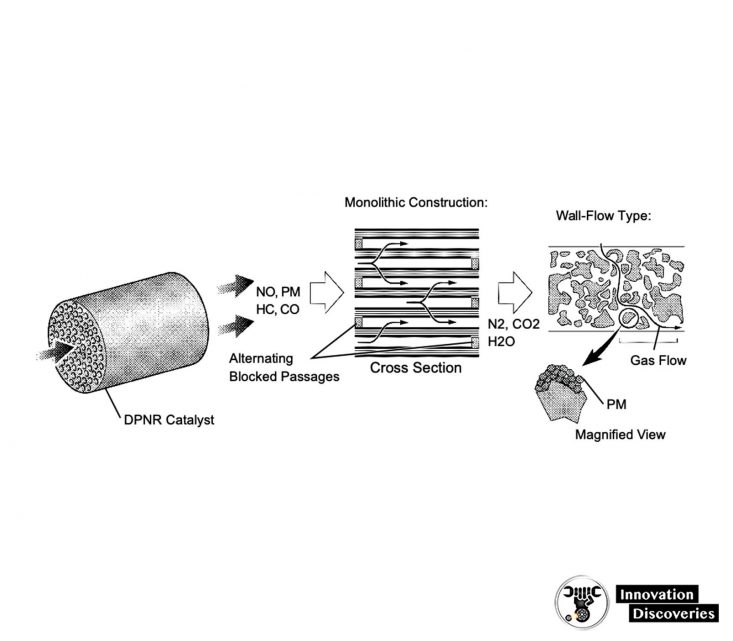
Exhaust Gas Temperature Sensor
The exhaust gas temperature sensors are installed before and after the DPNR catalytic converter to sense the exhaust gas temperature.
A thermistor built into the exhaust gas temperature sensor changes resistance value in accordance with changes in the exhaust gas temperature.
The lower the exhaust gas temperature, the higher the thermistor resistance value. Conversely, the higher the exhaust gas temperature, the lower the thermistor resistance value.
The exhaust gas temperature sensor is connected to the ECU.
The 5 V power source voltage in the ECU is applied to the exhaust gas temperature sensor from terminals THCI (B1S1) and THCO (B1S2) via resistor R.
Resistor R and the exhaust gas temperature sensor are connected in series.
When the resistance value of the exhaust gas temperature sensor changes in accordance with the exhaust gas temperature, the voltage at terminals THCI (B1S1) and THCO (B1S2) also change.
When DPNR catalyst regeneration is needed, the ECU operates the exhaust fuel addition injector to obtain the target upstream temperature for the DPF catalytic converter (as monitored through sensor 1). In addition, the ECU monitors the temperature increase of the DPNR catalytic converter using sensor
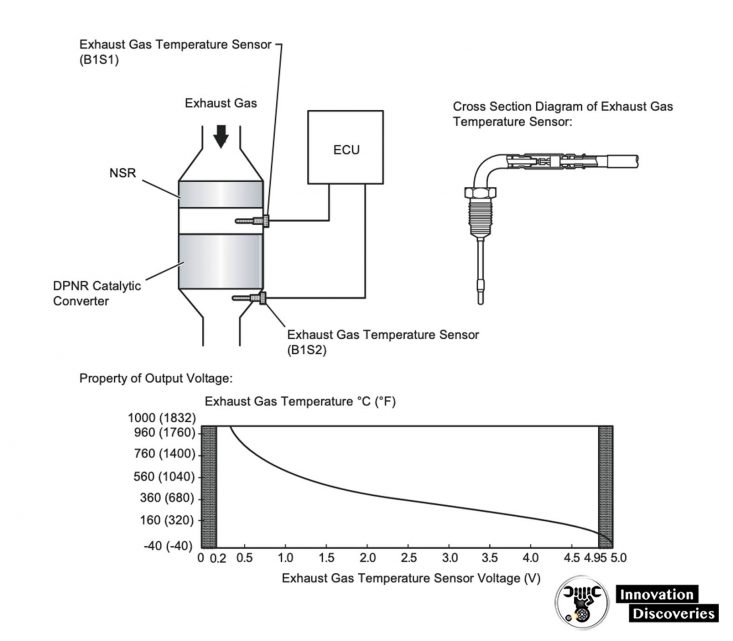
Differential Pressure Sensor
The differential pressure sensor detects the difference in pressure at the front and rear of the catalyst and outputs a signal to the engine ECU.
The sensor portion is a semiconductor-type pressure sensor that utilizes the piezoelectric effect via a silicon element and amplifies and outputs a voltage with an IC circuit.
When PM is collected and accumulated in the catalyst, the filter clogs and the difference in pressure at the front and rear of the catalyst increases.
Therefore, the engine ECU judges whether or not to subject the PM to combustion processing based on the sensor signals.
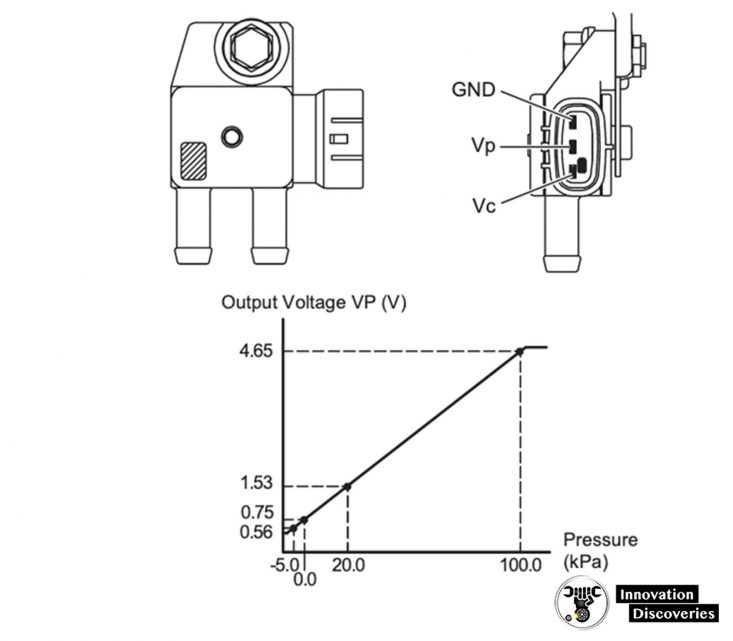
A/F Sensor
The A/F sensor outputs a voltage* that is proportional to the air-fuel ratio.
The A/F sensor output voltage is used to control the A/F mixture. A/F sensor is located after the DPNR catalytic converter.
A/F sensor was developed based on the structure and technology of the A/F sensor used in gasoline engines.
The cover for the A/F sensor electrode has been modified for diesel engine use.
As a result, the A/F sensor functions more effectively in the DPNR type diesel engine, and also avoids problems with sensor temperature and PM.
To reduce PM, the ECU adjusts the air-fuel ratio to a value slightly richer than normal (note that this mixture is still leaner than the stoichiometric air-fuel ratio.)
The ECU controls the aforementioned adjustments based on signals from the A/F sensor.
When the ECU performs DPNR catalyst regeneration (cleaning) by adding fuel from the exhaust fuel addition injector, the A/F sensor feedback is used to ensure that an appropriate air-fuel ratio is maintained.
*: This voltage change occurs only inside the ECU. It is not possible to measure this voltage at the sensor.
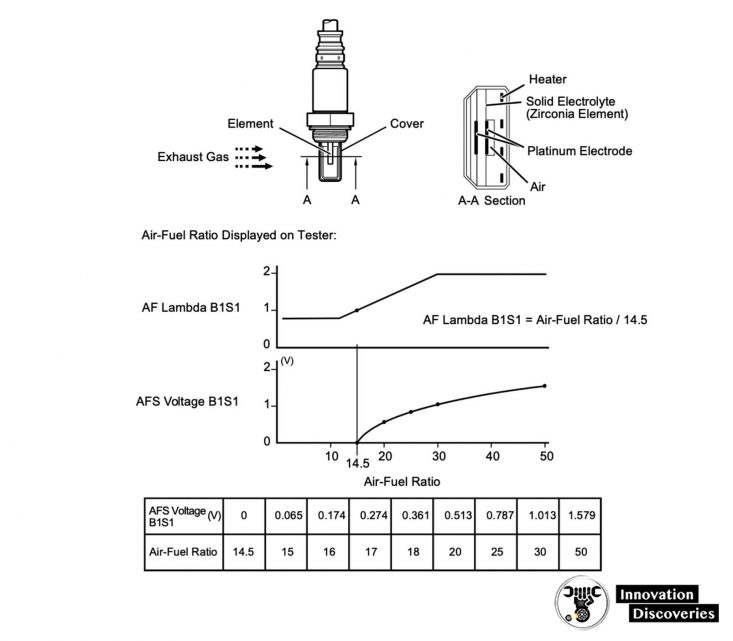
Exhaust Fuel Addition Injector
The exhaust fuel addition injector receives signals from the engine ECU and controls the catalyst A/F and temperature in accordance with the CPU program.
A pre-determined amount of fuel is injected from the injector into the exhaust gas pipes during pre-determined conditions.
As shown below, the exhaust fuel addition injector is installed on the engine exhaust side, and fuel from the supply pump is sent through the pipe.
A pressure of 1 MPa is constantly applied to the exhaust fuel addition injector.
The exhaust fuel addition injector receives output signals from the ECU (time variable pulse) to generate an electromagnetic force in the interior coil.
As a result, the needle moves left and right, thus moving the valve body integrated with the needle in the same direction.
As such, fuel is injected from the nozzle.
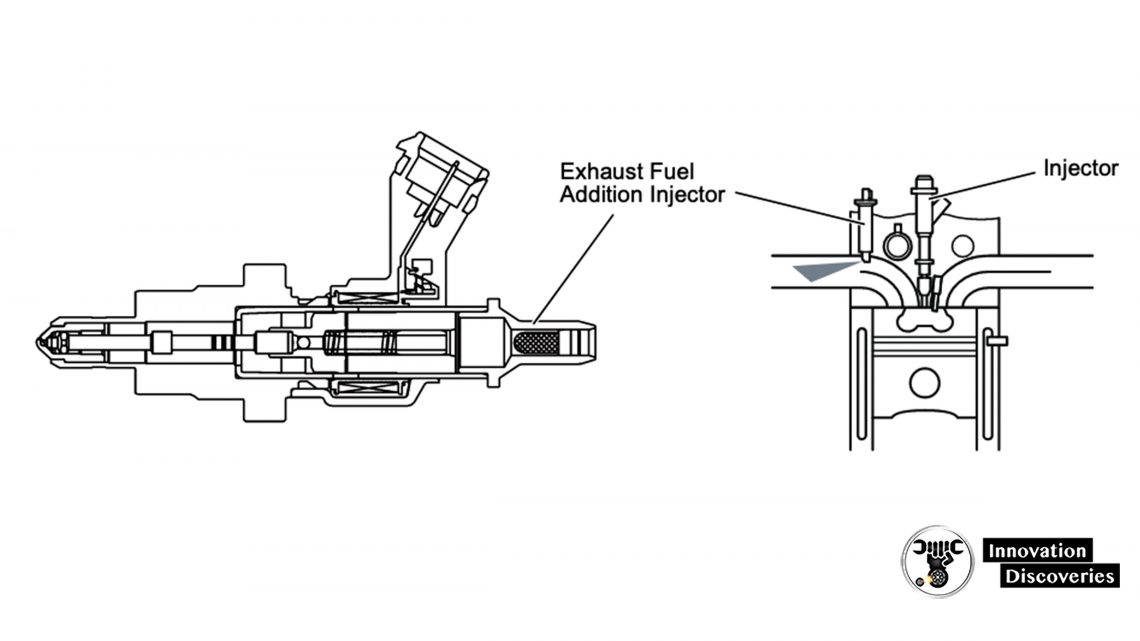
The exhaust fuel addition injector is mounted on the exhaust port of the cylinder head, and low-pressure fuel is provided to the injector by the feed pump inside the supply pump.
Fuel is added from this injector via control signals from the ECU to perform catalyst regeneration.
During catalyst regeneration, the exhaust fuel addition injector adds fuel to raise the catalyst temperature.
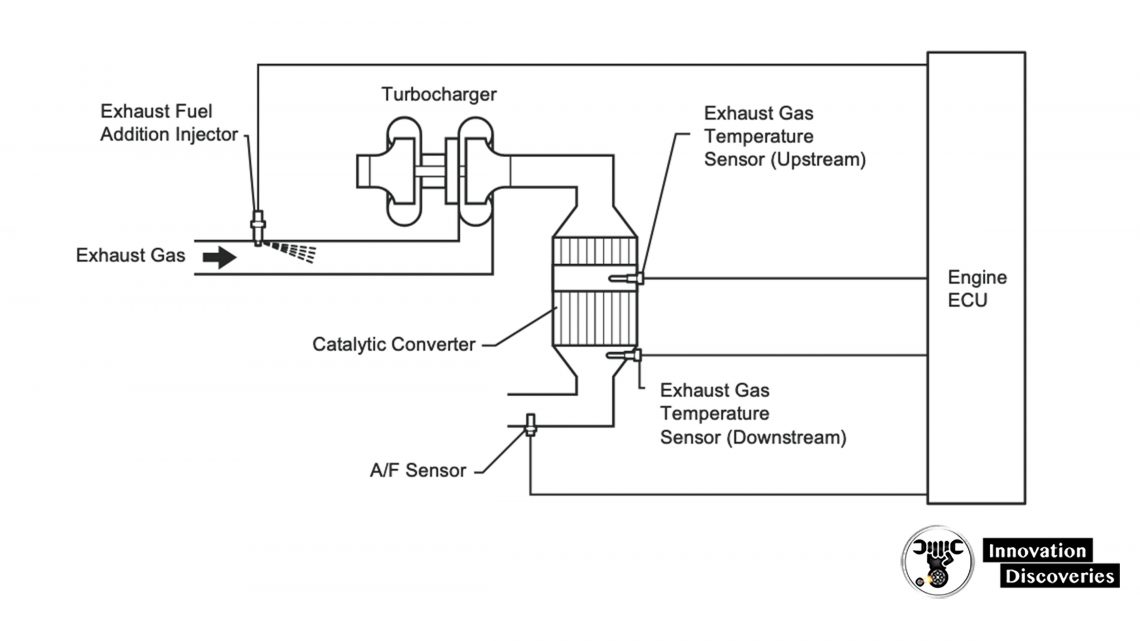
Continuous PM regeneration, and NOx reduction
The D-CAT system is a combination of an NOx adsorption three-way catalyst and a porous ceramic construction.
As exhaust gas passes through the gaps in the porous ceramic construction, the catalyst oxidizes the PM, and reduces the NOx, drastically reducing the quantity of both substances.
Lean combustion (excessive oxygen state) is normally performed in diesel engines. In a lean state, oxidation occurs easily, but a reduction is difficult to produce.
Therefore, it is necessary to temporarily adsorb NOX with the DPNR catalyst.
When the NOx is adsorbed, PM oxidation is promoted by the generation of active oxygen.
To reduce the NOx, first fuel is injected by the exhaust fuel addition injector to create a rich state (where the quantity of oxygen is relatively small).
In this rich state, NO, as well as a large quantity of active oxygen are generated by the NSR and DPNR catalysts.
The NO is then reduced to N2, and the PM is oxidized by the active oxygen. As a result, NOx and PM are simultaneously reduced.
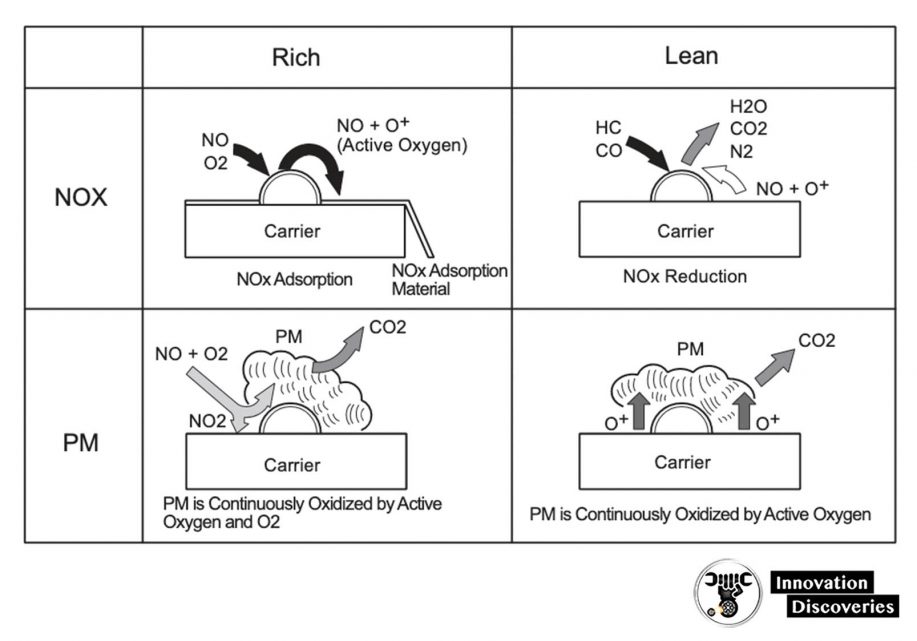
S (Sulfur) regeneration
When sulfur contained in the diesel fuel accumulates in the catalyst, NOx purification capacity decreases.
S regeneration is used to restore the NOx purification capacity.
By injecting fuel into the catalyst using the exhaust fuel addition injector, the air-fuel ratio in the catalyst can be made rich, and the catalyst temperature can be raised (to 650°C).
As a result, the sulfur from the fuel temporarily accumulated in the catalyst is eliminated.
S regeneration control is performed simultaneously with PM regeneration control. When S regeneration takes place, the idling rotational speed increases.
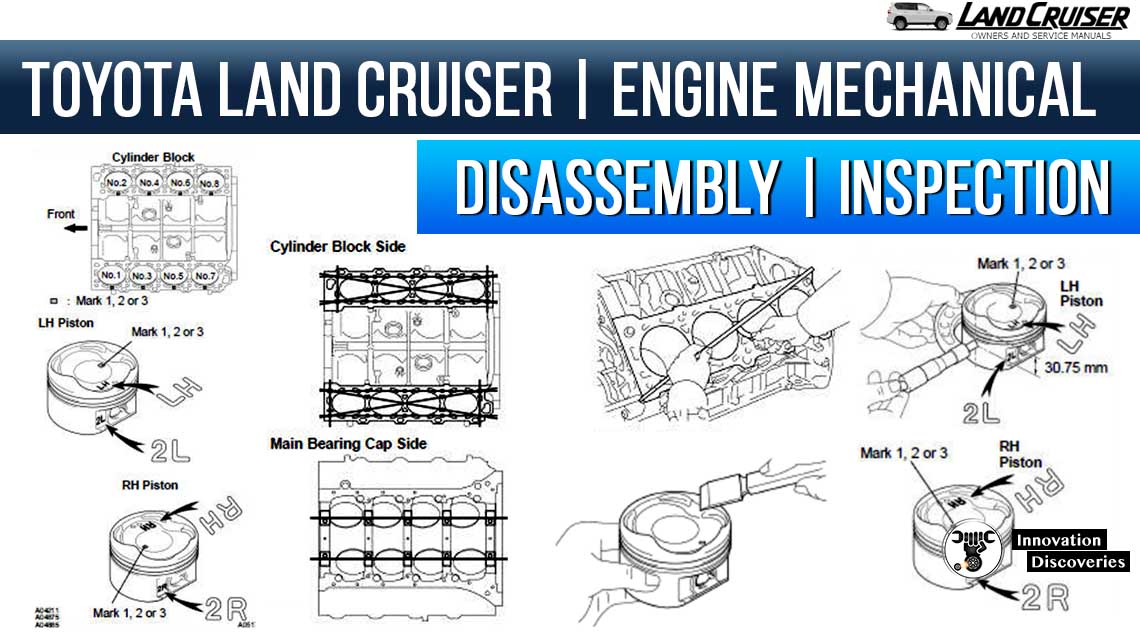
Visit Forum
Visit Our Friendly Website

One Comment