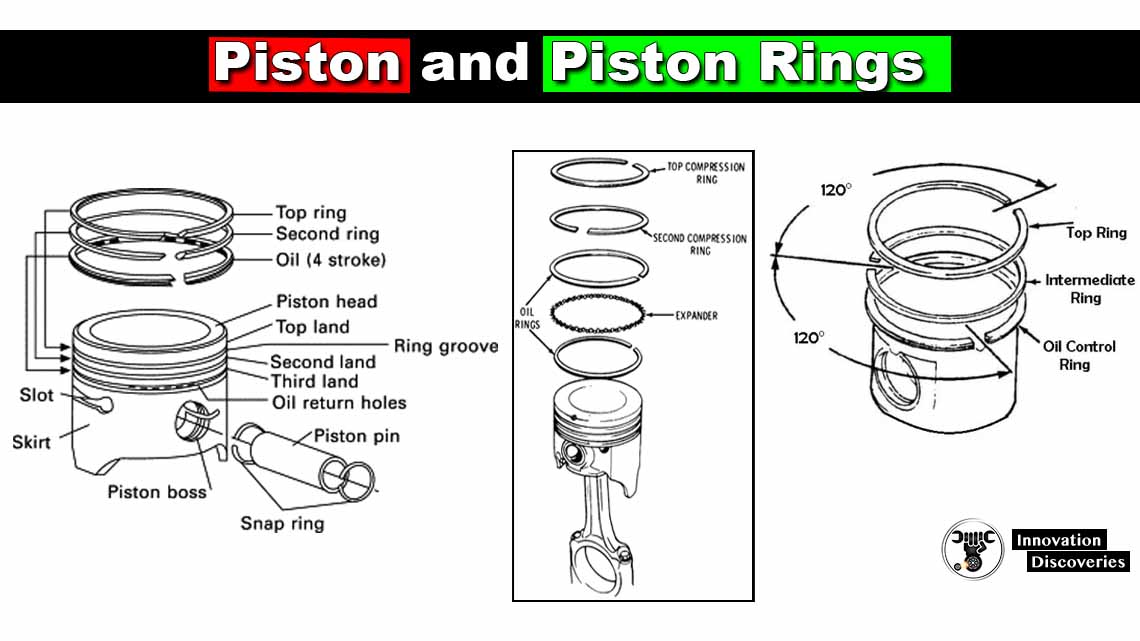
In the realm of internal combustion engines, pistons and piston rings play vital roles in converting combustion energy into mechanical motion. These components are central to engine efficiency, durability, and performance. Their engineering design directly impacts fuel consumption, emissions, and overall engine longevity.
Piston: Structure and Functionality
Role in the Engine
The piston is a cylindrical component that reciprocates within the engine cylinder. It transforms the force generated by the combustion of the air-fuel mixture into mechanical motion. This linear motion is transmitted to the crankshaft via the connecting rod, ultimately producing the rotary power that drives the vehicle.
Materials and Thermal Considerations
Pistons are typically made from cast aluminum alloys due to their lightweight properties and excellent thermal conductivity. Aluminum dissipates heat effectively, maintaining a stable engine operating temperature. However, its thermal expansion requires tight engineering tolerances to avoid engine knock or piston seizure.
Key Components of a Piston
- Piston Head (Crown): The upper surface directly exposed to combustion forces and heat.
- Piston Pin Bore: A horizontal bore to house the piston pin, which connects the piston to the connecting rod.
- Piston Pin (Gudgeon Pin): A hollow shaft that facilitates the pivoting motion between the piston and the rod.
- Skirt: The lower part of the piston that guides its movement within the cylinder and helps maintain alignment.
- Ring Grooves: Recessed sections designed to accommodate piston rings.
- Ring Lands: The areas between ring grooves that provide structural support and sealing surfaces for the rings.
Piston Rings: Types and Functions
Piston rings are precision-engineered split rings that fit snugly into the grooves near the top of the piston. Though small in size, they play a crucial role in the overall performance and efficiency of an internal combustion engine. Their core functions include:
- Sealing the Combustion Chamber
Piston rings create a tight seal between the piston and the cylinder wall, preventing high-pressure combustion gases from leaking into the crankcase. This ensures maximum power output and fuel efficiency. - Regulating Oil Consumption
By scraping excess oil from the cylinder walls during each stroke, piston rings help maintain proper lubrication while preventing oil from entering the combustion chamber—minimizing oil consumption and exhaust smoke. - Transferring Heat
Piston rings conduct heat away from the hot piston to the cooler cylinder walls. This heat transfer is vital to preventing piston overheating, distortion, and potential engine damage.
1. Compression Ring
The compression ring is the topmost piston ring, situated closest to the piston crown. It plays a crucial role in maintaining engine efficiency and performance by forming a tight seal between the piston and the cylinder wall.
Primary Function
Its main job is to seal the combustion chamber, preventing high-pressure gases produced during the combustion stroke from escaping into the crankcase. By containing the gas pressure above the piston, the compression ring ensures that maximum force is transferred to the piston during power strokes.
Design Considerations
Compression rings must withstand extreme temperatures and high pressure, often reaching over 2000 psi in modern engines. They also encounter significant friction as they rub against the cylinder wall. As such, they’re typically made from high-strength cast iron or steel alloys, and often coated for improved durability.
Common Design Variations
- Taper-Faced Compression Ring
- Features a slight taper on the outer face.
- Improves initial sealing by enhancing the contact angle between the ring and the cylinder wall.
- Helps scrape a thin layer of oil downward during piston movement.
- Barrel-Faced Compression Ring
- Has a convex outer surface (barrel shape).
- Ensures more uniform contact pressure throughout the piston stroke.
- Reduces wear and blow-by by maintaining better sealing under varying operating conditions.
- Rectangular Cross-Section Ring
- Common in many standard engines.
- Offers good sealing but may not be as wear-resistant under high-performance loads as tapered or barrel-faced types.
Performance Characteristics
- Sealing Efficiency: Critical for maintaining compression ratio and engine power output.
- Heat Transfer: Helps conduct heat from the piston to the cooler cylinder wall, preventing overheating.
- Blow-by Control: Prevents unburned fuel and exhaust gases from escaping into the crankcase, which could dilute engine oil and reduce lubrication quality.
2. Wiper Ring (Scraper Ring)
The wiper ring, also known as the scraper ring, is positioned just below the compression ring in a piston’s ring groove stack. While it does contribute to combustion sealing, its primary purpose is oil regulation, ensuring that only a fine film of oil remains on the cylinder walls.
Primary Function
The wiper ring scrapes excess lubricating oil off the cylinder walls during the piston’s downward stroke. This prevents too much oil from entering the combustion chamber, which would otherwise result in oil burning, carbon deposits, and increased emissions.
It also acts as a secondary seal against combustion gases, supporting the compression ring by handling any blow-by that might pass it.
Design Considerations
Wiper rings are subjected to both mechanical friction and thermal loads, although not as intense as the compression ring. Their edge geometry and surface finish are specifically engineered for optimal oil scraping and wear resistance.
They’re generally manufactured from the same materials as compression rings—ductile cast iron or alloy steel—and are frequently coated with materials like molybdenum or chromium for improved durability and reduced friction.
Common Design Variations
- Napier Ring
- Features a hook or step-shaped profile on the bottom edge.
- Enhances oil scraping ability while maintaining a sealing edge for combustion gases.
- Especially effective in controlling oil in high-speed or turbocharged engines.
- Taper-Faced Wiper Ring
- Has a slight taper on its face, aiding in both oil scraping and backup compression sealing.
- Simple but effective design used in many OEM and aftermarket pistons.
- Positive Twist Ring
- Designed with a built-in twist that increases radial pressure when compressed during installation.
- Improves contact with the cylinder wall during operation, promoting more aggressive oil scraping.
Performance Characteristics
- Oil Control: Ensures the right amount of oil remains on the cylinder wall—enough for lubrication but not enough to burn.
- Sealing Support: Assists the compression ring in minimizing gas blow-by.
- Wear Resistance: Must maintain scraping efficiency over thousands of operating hours without scoring or damaging the cylinder wall.
- Thermal Stability: Should perform consistently under varying temperature cycles, particularly during cold starts and high-load conditions.
3. Oil Control Ring
The oil control ring is the lowest ring on the piston and plays a crucial role in the lubrication system of an internal combustion engine. Its job is not to seal combustion gases, but rather to regulate the oil film thickness on the cylinder walls.
Primary Function
The oil control ring is responsible for:
- Scraping excess lubricating oil off the cylinder walls during the piston’s stroke.
- Allowing a precise, thin oil film to remain for proper lubrication.
- Preventing oil from migrating into the combustion chamber, thereby reducing oil burning, smoke emissions, and carbon buildup on valves and spark plugs.
By maintaining the correct oil film, the oil control ring also helps cool the piston and reduce friction between the piston and cylinder wall.
Design and Construction
Unlike the compression and wiper rings, the oil control ring is often a multi-piece assembly, engineered for flexibility, tension control, and high oil-scraping efficiency.
Common Design Variations
- Two-Piece Oil Ring
- Consists of two components:
- A single-piece ring (usually steel or cast iron)
- A spacer-expander placed underneath to ensure outward tension.
- Simpler in construction but still effective in many standard engines.
- Consists of two components:
- Three-Piece Oil Control Ring
- The most widely used modern oil control ring design.
- Composed of:
- Two thin steel rails (upper and lower)
- One expander/spacer in the middle (usually wavy or slotted steel).
- Offers excellent flexibility and superior oil regulation, especially in high-speed or high-performance engines.
Material and Coating
- Made from high-tensile steel or ductile cast iron.
- Often coated with chrome, molybdenum, or nitrided layers to enhance wear resistance, reduce friction, and ensure long-term reliability.
Key Performance Attributes
- Lubrication Control: Ensures engine components remain lubricated without excess oil consumption.
- Friction Reduction: Reduces drag by maintaining optimal oil thickness, contributing to better fuel economy.
- Emission Control: Limits the entry of oil into the combustion chamber, thereby reducing blue smoke and carbon emissions.
- Durability: Designed to last over extended engine cycles without significant wear or distortion.
Ring Type | Location on Piston | Primary Function | Common Designs |
---|---|---|---|
Compression Ring | Topmost | Seals combustion gases | Taper-faced, Barrel-faced |
Wiper Ring | Middle | Scrapes excess oil & supports sealing | Napier, Positive Twist |
Oil Control Ring | Bottom | Regulates oil on cylinder walls | Two-piece, Three-piece (rail + expander) |
Click to read: PISTON DAMAGE FROM OVERHEATING
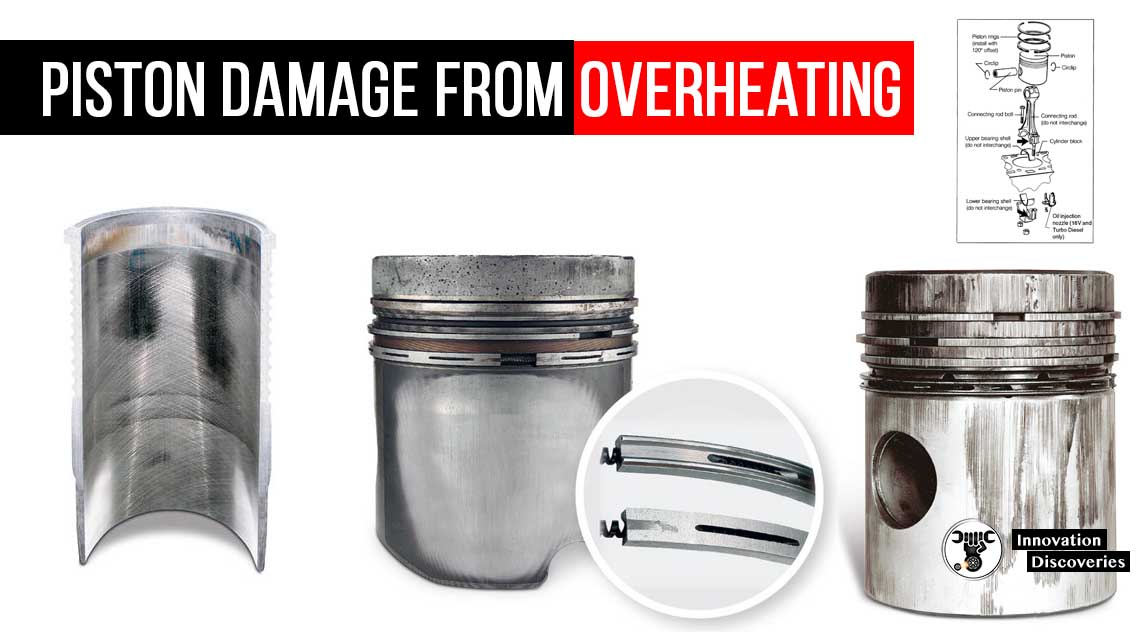
Materials and Coatings
Base Materials
- Cast Iron: Offers excellent wear resistance and thermal stability, widely used in standard applications.
- Steel: Preferred in high-performance engines due to its superior strength and heat resistance.
Common Coatings
- Chromium: Enhances wear resistance and minimizes friction.
- Molybdenum: Provides strong lubrication retention and wear resistance.
- Ceramic or Polymer Compounds: Improve heat resistance and reduce friction in advanced engines.
Technical Specifications
Dimensions
- Width: Typically ranges from 1.5 mm to 3 mm depending on the engine design.
- Thickness: Between 0.5 mm and 1.5 mm, influencing strength and sealing effectiveness.
Radial Gap
The radial clearance between the piston ring and the cylinder wall is crucial for gas sealing and oil control. Standard gaps range from 0.1 mm to 0.5 mm.
Hardness
Piston rings generally measure between 35 to 55 HRC on the Rockwell scale. This range provides an optimal balance of durability and flexibility.
Advanced Materials and Coatings
To meet the demands of modern internal combustion engines—especially those that operate under high stress, temperature, and speed—advanced materials and coatings have become vital in the design of pistons and piston rings. These innovations not only enhance durability but also improve engine performance, fuel efficiency, and emissions control.
1. Advanced Base Materials
While traditional piston rings are commonly made from cast iron or alloy steel, newer engines are adopting specialized materials that can withstand extreme operating conditions:
- Ductile Cast Iron (Nodular Iron):
Offers greater elasticity and crack resistance compared to gray cast iron. Ideal for high-load applications. - High-Strength Steel Alloys:
Used in performance and heavy-duty engines for their superior tensile strength, wear resistance, and dimensional stability at elevated temperatures. - Powder Metallurgy Alloys:
Enable precision in material composition and structure. Often used in customized ring designs for high-performance or racing applications.
2. Coating Technologies
Modern coating technologies are applied to both pistons and rings to reduce friction, control wear, and improve heat resistance. Common coatings include:
Chromium (Chrome-Plating)
- Provides a hard, wear-resistant surface.
- Excellent for oil control rings.
- Reduces scuffing and friction in dry-start conditions.
- Bright appearance; often seen on compression rings.
Molybdenum (Mo)
- Usually applied as a plasma-sprayed or electroplated coating.
- Excellent lubricity and heat resistance.
- Retains oil well, reducing metal-to-metal contact.
- Commonly used in compression rings of high-load engines.
Phosphate Coating
- Offers corrosion protection during initial engine startup.
- Acts as a base layer to improve adhesion of lubricants.
- Mostly seen on piston rings during engine assembly and break-in.
Nitriding
- A surface-hardening process that infuses nitrogen into the metal surface.
- Increases surface hardness without altering core properties.
- Offers superior wear and fatigue resistance.
3. Next-Gen Coatings and Innovations
The push for greater efficiency and lower emissions has led to the emergence of cutting-edge surface treatments and composite coatings:
Graphene-Based Coatings
- Ultra-thin and thermally conductive.
- Offers superior wear resistance and low friction.
- Still in early phases of adoption but showing promising results in prototype engines.
Nickel-Phosphorus with MoS₂ (Ni-P-MoS₂)
- A hybrid coating combining nickel-phosphorus plating with molybdenum disulfide (solid lubricant).
- Significantly reduces friction and improves wear performance.
- Ideal for turbocharged and downsized engines.
Ceramic Composite Coatings
- Used especially in racing or aerospace piston designs.
- Extreme heat resistance and low thermal expansion.
- High cost, but very effective in thermal barrier applications.
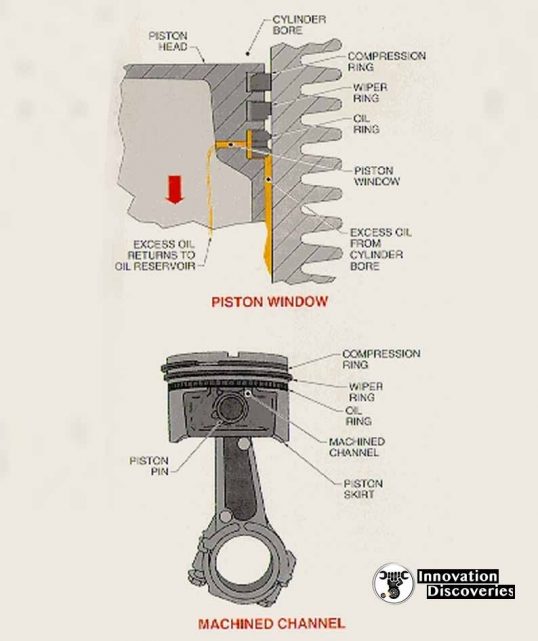
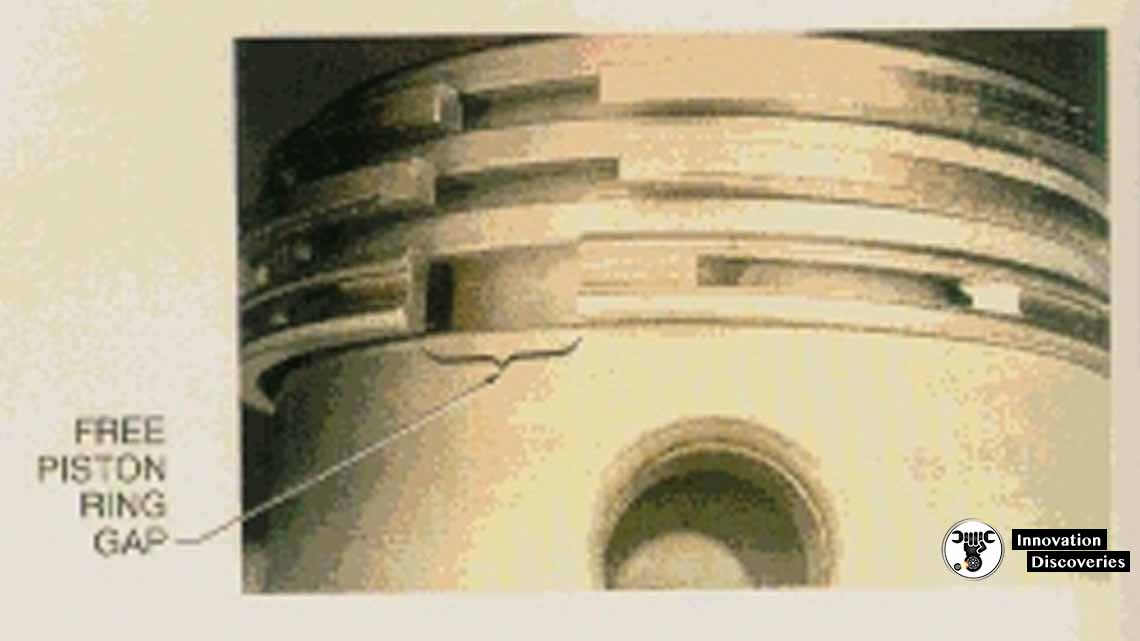
Key Benefits of Advanced Materials and Coatings:
Feature | Benefit |
---|---|
Wear Resistance | Longer engine life and better performance |
Heat Resistance | Withstands high combustion temperatures |
Friction Reduction | Improves efficiency and reduces fuel usage |
Lubrication Retention | Supports smoother piston movement |
Emissions Reduction | Less oil burning and cleaner combustion |
These advancements reflect the industry’s continuous drive toward stronger, smarter, and more efficient internal engine components. By combining material science with precision engineering, modern piston and ring systems can now meet the high expectations of performance, durability, and sustainability.
Historical Perspective
The use of piston rings dates back to the mid-1800s when Bulgarian inventor Nikola Toshkovich introduced elastic rings to improve piston-to-cylinder sealing. This innovation significantly enhanced engine reliability and efficiency and laid the foundation for modern engine designs.
Conclusion
Pistons and piston rings are foundational to the performance and reliability of internal combustion engines. Their structure, materials, and function influence everything from fuel efficiency to emissions. As engines evolve to meet stricter performance and environmental standards, so too do the designs and materials of these critical components. A deep understanding of their engineering is essential for anyone involved in engine design, maintenance, or performance tuning.
See More:
- 3 Symptoms of Bad Valve Seals and Piston Rings and Replacement Cost
- What Is Blow-By On A Diesel Engine And Its Causes?
More About Braking Systems
- Top 5 Causes of Steering Wheel Shakes at Low and High Speeds
- HOW HYDRAULIC BRAKE WORKS?
- AIR BRAKE SYSTEM: COMPONENTS, WORKING PRINCIPLE, AND APPLICATIONS
- HOW DOES REGENERATIVE BRAKING WORK?
- 8 REASONS YOUR CAR IS MAKING GRINDING NOISE WHEN BRAKING
- Regenerative Braking System
- JAKE BRAKE VS. EXHAUST BRAKE: WHICH IS BETTER?
- SQUEALING BRAKES AT LOW SPEED: CAUSES AND SOLUTIONS
- TROUBLESHOOTING A HARD BRAKE PEDAL
- CONVERT DRUM BRAKES TO DISC BRAKES IN 3 STEPS!
- CAUSES OF THE BRAKE WARNING LIGHT COMING ON
Visit Forum
Visit Our Friendly Website

2 Comments