Timing Mark
The timing mark is an arbitrary alignment point shared by the engine case and stator plate.
It indicates the purpose at which the highest of the piston’s travel is like the
Trigger point on the flywheel and stator.
By rotating the stator plate left and right,
You effectively change the trigger point of the CDI,
Thus advancing or retarding your timing, respectively. Because the flywheel turns fast,
The charging coil produces an AC from +6V to -6V.
The CDI box features a collection of semiconductor rectifiers that connected to
G1 on the box allows only the positive pulse to enter the capacitor (C1).
While the wave getting into the CDI, the rectifier allows only the positive wave.
Trigger Circuit
The trigger circuit may be a switch, probably employing a Transistor,
Thyristor or SCR. This triggered by a pulse from the Hall Sensor on the stator.
They only allow current from one side of the circuit until they’re triggered.
Once the Capacitor C1 is fully charged, the circuit is often triggered again.
This is often why there’s timing involved in the motor. If the capacitor and stator were perfect,
They might charge instantaneously and that we can trigger them as fast as our wish. However, they require a fraction of a second to full charge.
If the circuit triggers too fast,
Then the spark from the sparking plug is going to be enormously weak. Certainly, with the upper accelerating motors,
We may have the triggering faster than the capacitor full charge,
Which can affect performance?
Whenever the capacitor is discharged,
Then the switch turns itself off and therefore the capacitor charges again.
The trigger pulse from the Hall sensor feeds into the gate latch and allows all the stored charge to rush through the first side of the high-voltage transformer. The transformer features a footing between the first and secondary windings, referred to as an autotransformer.
Therefore, as if we increase the windings on the secondary side, you’ll multiply the voltage. Since a sparking plug needs an honest 30,000 volts to sparks,
There must be many thousands of wraps of wire round the high voltage or secondary side.
When the gate opens and dumps all the present into the first side,
It saturates the low-voltage side of the transformer and sets up a brief but immensely magnetic flux. Because the field reduces gradually,
An outsized current within the primary windings forces the secondary windings to supply extremely high voltage.
However, the voltage is now so high that it can arc through the air,
So instead of being absorbed or retained by the transformer,
The charge travels up the plug wire and jumps the plug gap.
When we want to pack up the motor engine, we’ve two switches the key switch or the kill switch. The switches ground out the charging circuit, therefore, the entire charging pulse is shipped to the bottom. Since the CDI can not charge,
It’ll cease to supply the spark and therefore the engine will slow to a stop.
Advantages of CDI
- The major advantage of CDI is that the capacitor can be fully charged in a very short time (typically 1ms). So the CDI is suited to an application where the insufficient dwell time is available.
- The capacitor discharge ignition system has a short transient response, a fast voltage rise (between 3 to 10 kV/ µs) compared to inductive systems (300 to 500 V/ µs) and shorter spark duration (about 50-80 µs).
- The fast voltage rising makes CDI systems unaffected to shunt resistance.
Disadvantages of CDI
- The capacitor discharge ignition system generates huge electromagnetic noise and this is the main reason why CDIs are rarely used by automobile manufacturers.
- The short spark duration is not good for lighting relatively lean mixtures as used at low power levels. To solve this problem many CDI ignitions release multiple sparks at low engine speeds.
Read More:
- Car Battery Or Alternator: Which One Is The Culprit Behind A Dead Car?
- Are you an ignition expert? Take the quiz!
- How To Tell If Starter Relay Is Bad? Four Common Symptoms
- Common Spark Plug Misfire Symptoms
- Difference Between SI engine and CI engine
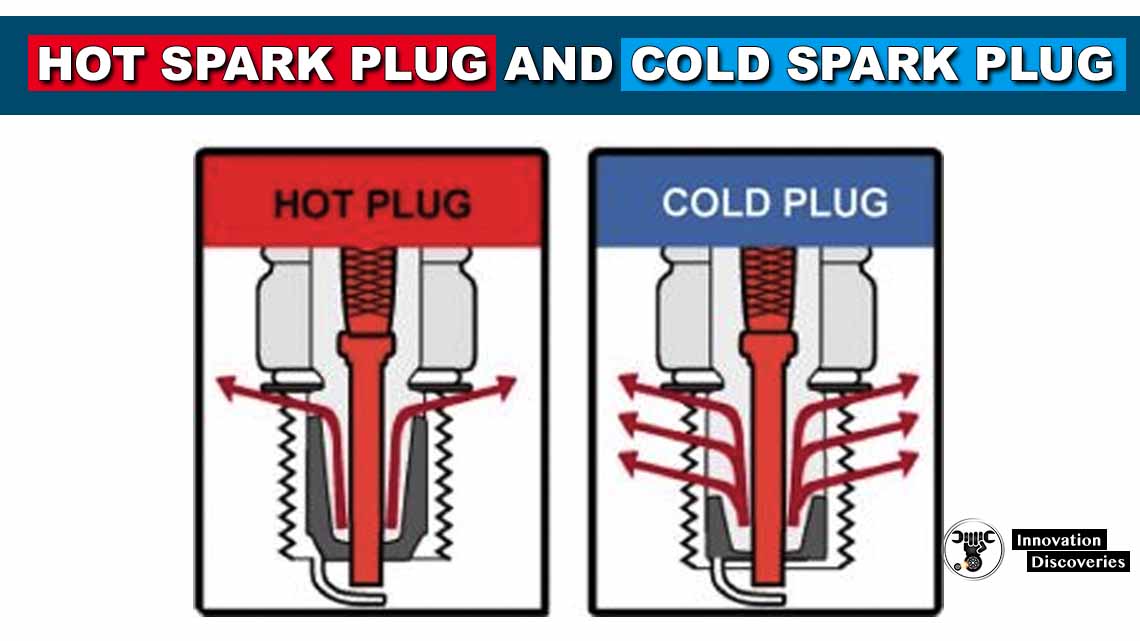
3 Comments