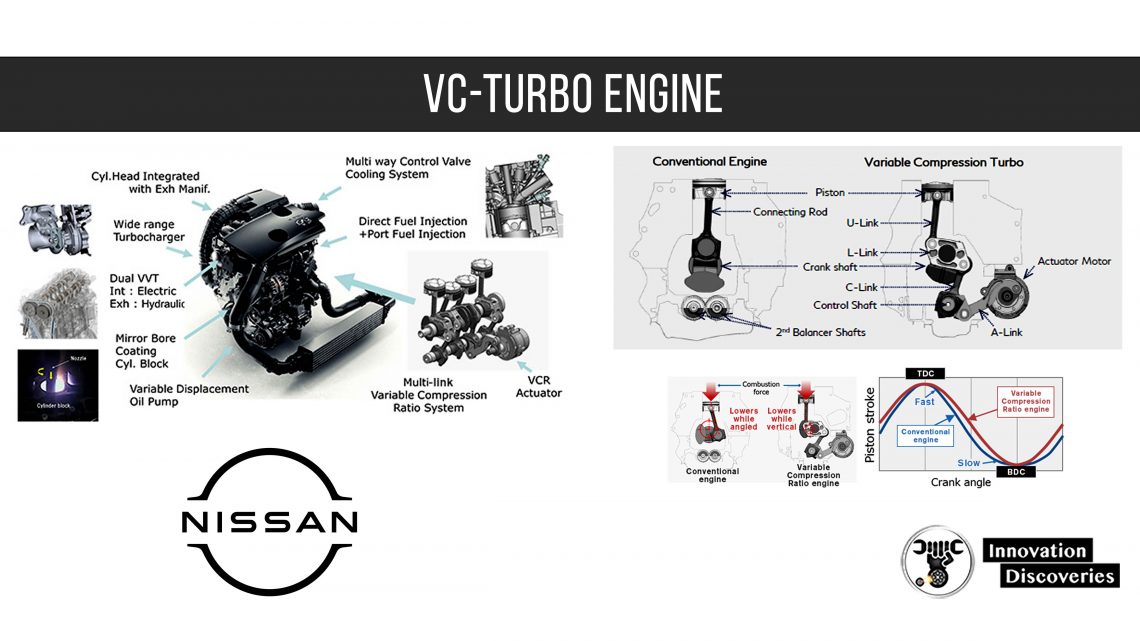
The VC-Turbo engine utilizes a multi-link system that continuously varies piston top dead center (TDC)?
bottom dead center (BDC) positions, allowing free control of the compression ratio critical factor of power and efficiency, on-demand.
This makes it the world’s first production engine to achieve both overwhelming high power and surprising fuel efficiency.
Two performance characteristics that ordinarily oppose each other.
System operation
• Making variable compression possible
A gasoline engine compresses an air-fuel mixture that enters into the cylinder before igniting and combusting it.
A higher compression ratio yields greater efficiency; however, there is a limit to the compression ratio because abnormal combustion (knocking) can occur due to the rise of mixture air temperature.
At cruising speeds when the intake airflow is low, the limit of compression ratio is high.
When accelerating, and the intake airflow is high, the limit is low.
Additionally, the limit becomes lower for a turbo engine that intakes compression air. It is ideal to change the compression ratio according to the load condition.
With a conventional engine, because the pistons and crankshaft are connected directly by the connecting rod, the compression ratio is fixed.
A VC-Turbo engine uses a multi-link system in place of a traditional connecting rod to rotate the crankshaft, and an actuator motor changes the multi-link system endpoint in order to vary the pistons’ reach to transform the compression ratio.
This makes it possible to vary the compression ratio continuously as needed within the range of 8:1 (for high load) to 14:1 (for low load).
The optimal compression ratio can be continuously set to match the operation of the accelerator pedal by the driver.
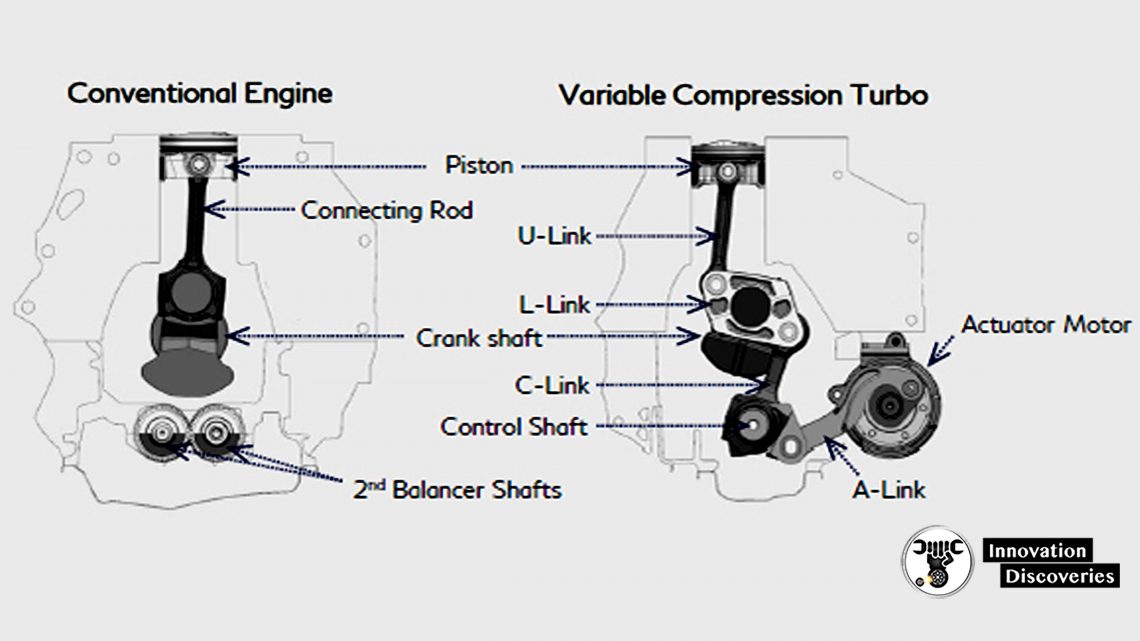
How it works
(1) When a change in the compression ratio is needed, the actuator motor moves the actuator arm.
(2) The actuator arm rotates the control shaft.
(3) The rotation of the control shaft moves the lower-link(L-link), changing the multi-link system angle.
(4) The multi-link system adjusts the vertical position of the piston stroke within the cylinder, changing the compression ratio.
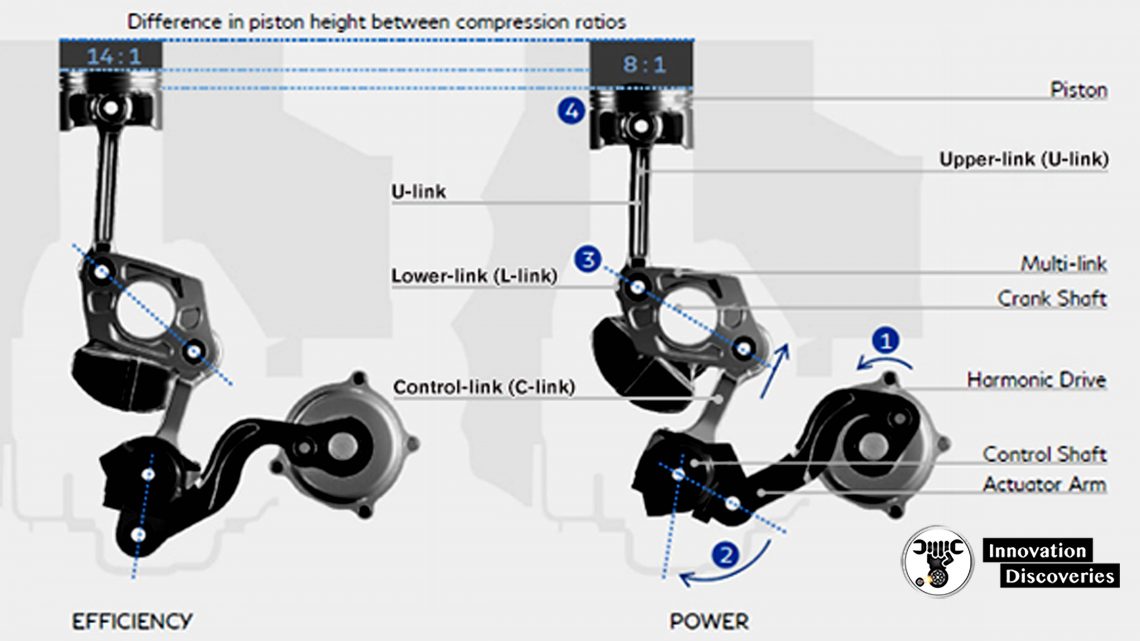
• Optimization of the link layout
As the angular change of the upper-link (U-link) when the piston moves up and down is small, the upper-link (U-link) remains more vertical as it moves down smoothly.
This reduces friction with the cylinder walls and contributes to improved fuel economy.
The reciprocating motion of the piston between TDC and BDC becomes symmetrical, helping to reduce vibration.
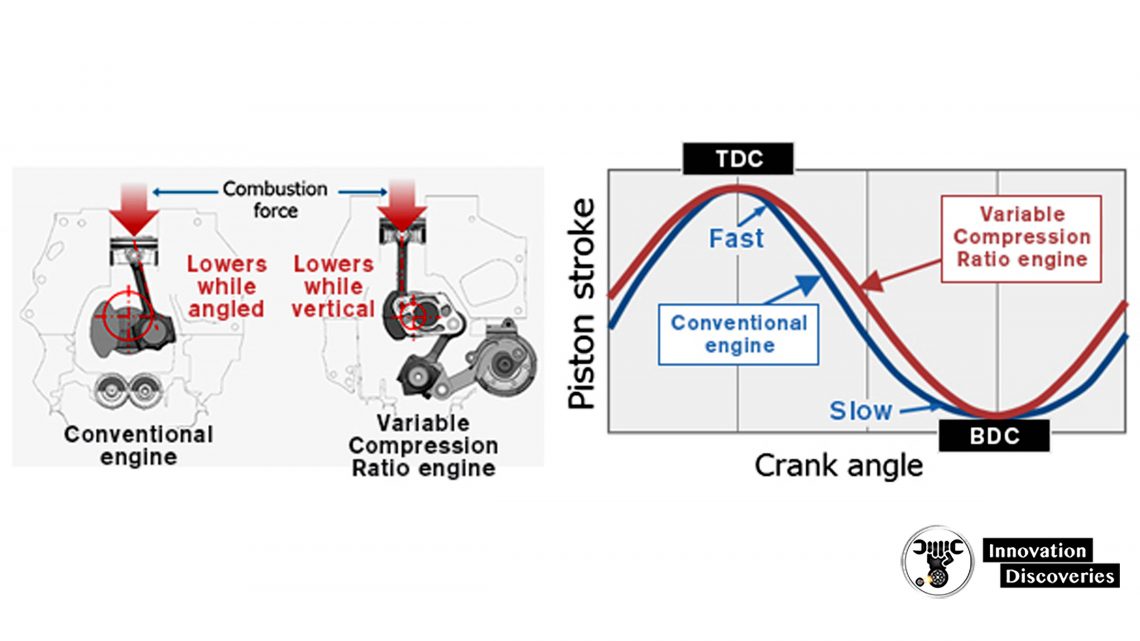
System mechanism
The VC-Turbo engine uses a newly developed high-efficiency, wide-range turbocharger, and electric wastegate.
This allows precise control of the boost pressure with minimal turbo lag to generate powerful on-demand output.
Under low load, the electric VTC (Valve Timing Control) continuously adjusts valve timing to reduce pumping loss through an Atkinson combustion cycle.
It realizes high fuel efficiency in combination with a higher compression ratio.
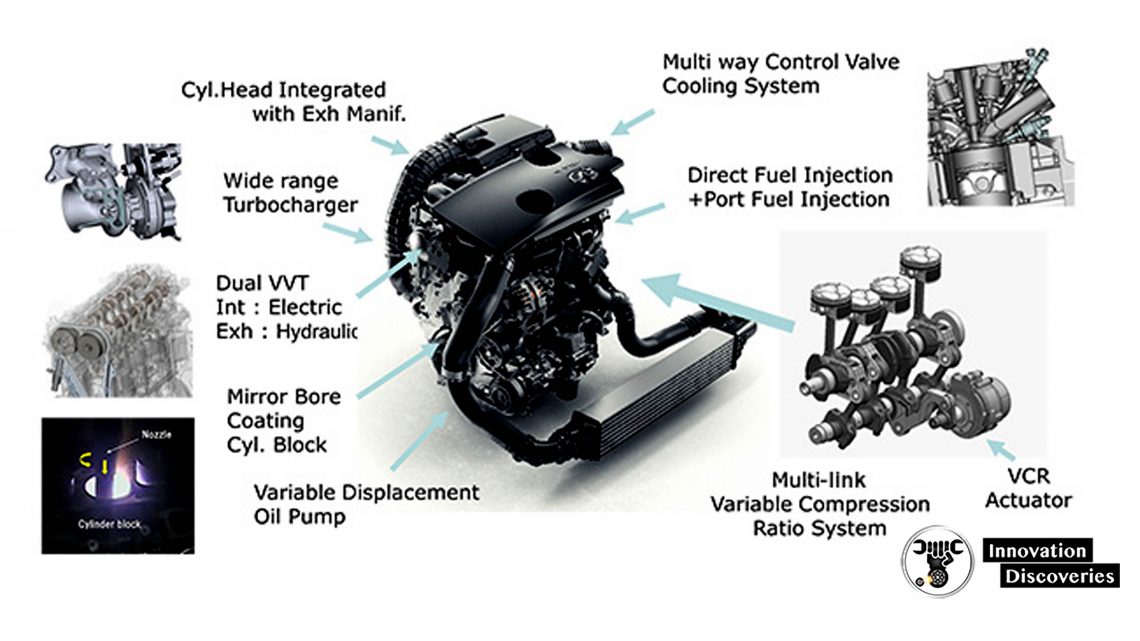
Research for VC-Turbo was started in 1998. Several methods were utilized to realize the VC-Turbo.
- Developing a variable compression system using a link mechanism
- Optimizing the link layout, using advanced analysis to produce precision part shapes
- Creating a new high-precision heat treatment were just a few technological hurdles.
As a result, Nissan became the world’s first auto manufacturer to start mass production of a variable compression engine.
READ MORE:
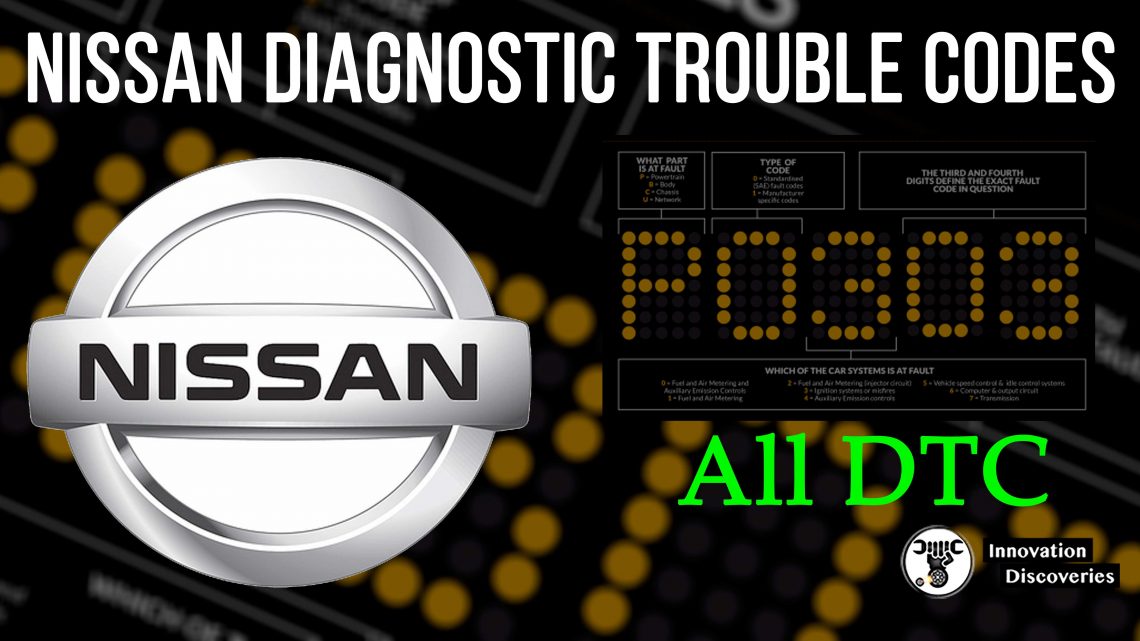
TURBOCHARGER: COMPONENTS, WORKING PRINCIPLES, AND TYPES
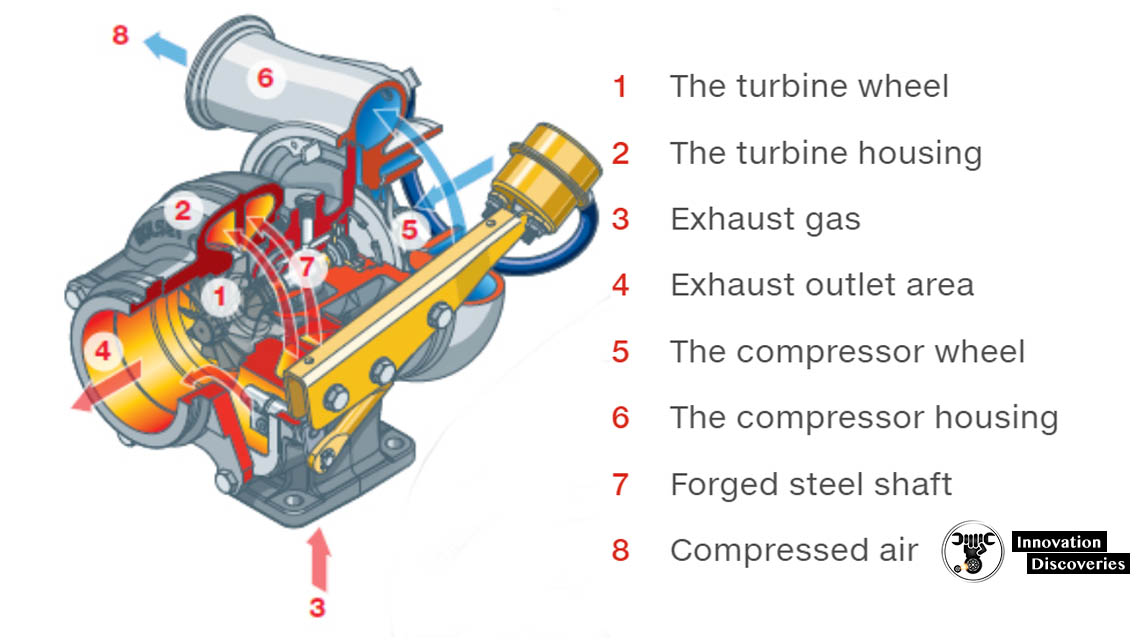
Visit Forum
Visit Our Friendly Website
