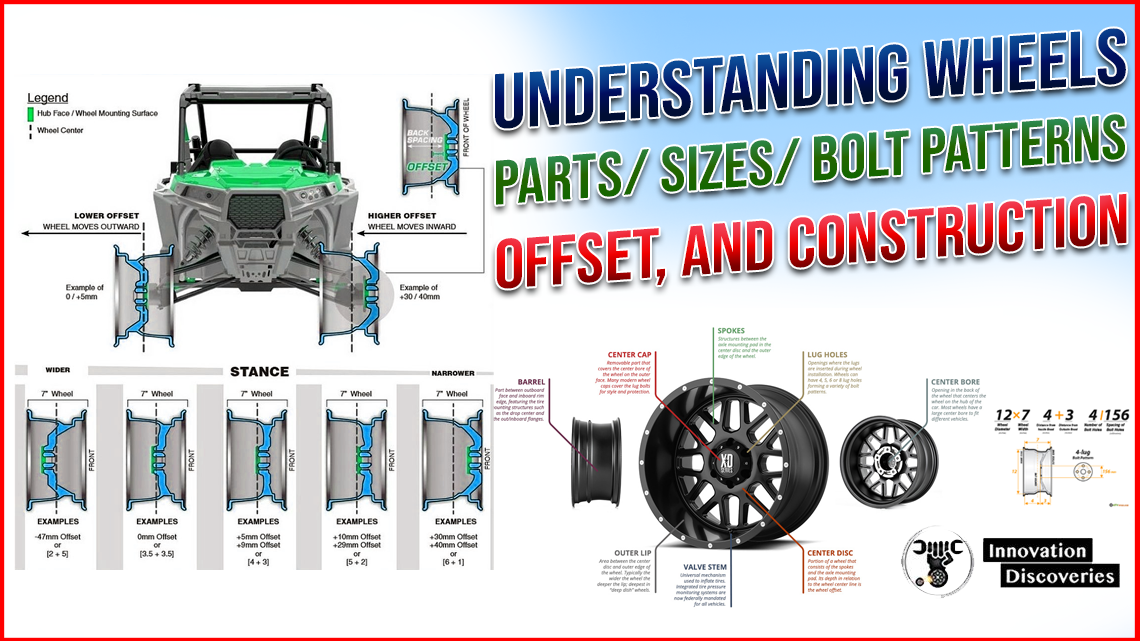
Wheels are an integral part of any vehicle, providing the crucial connection between the vehicle and the road. They not only support the weight of the vehicle but also contribute to its overall aesthetics and performance. Understanding the different aspects of wheels, such as their parts, sizes, bolt patterns, wheel offset, and the difference between one-piece and two-piece wheels, is essential for automotive enthusiasts and those looking to enhance their vehicle’s appearance and performance. Additionally, exploring the manufacturing process sheds light on the intricate craftsmanship involved in producing these essential components.
PARTS OF A WHEEL
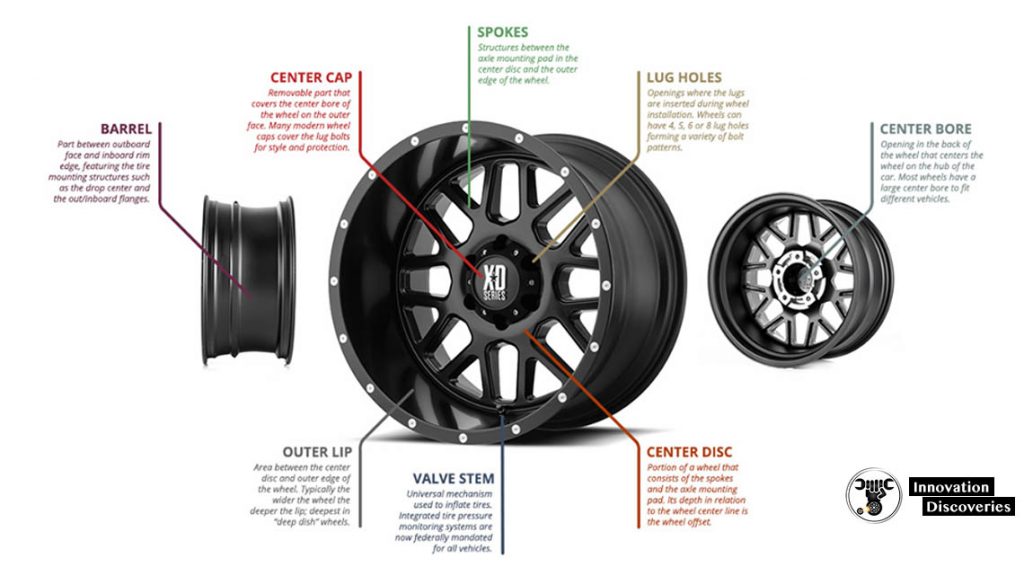
A wheel consists of several key components that work together to provide stability and functionality. These parts include the rim, tire, valve stem, center bore, lug nuts or bolts, and wheel weights. The rim forms the outer edge of the wheel and provides support for the tire. The tire, made of rubber and reinforced with various materials, is responsible for providing traction and absorbing shocks. The valve stem allows for tire inflation and deflation, while the center bore ensures proper alignment with the vehicle’s hub. Lug nuts or bolts secure the wheel to the vehicle, and wheel weights balance the assembly for smoother operation.
Read More: Why Tractors Have Bigger Rear Wheels & Smaller Front Wheels?
Focus bore
Wheel hub bore, also known as center bore or hub-centric bore, is the central hole on the backside of a wheel that fits over the vehicle’s hub assembly. It plays a vital role in ensuring proper fitment, stability, and optimal performance of vehicle wheels.
Hub-centric design provides several advantages, including enhanced stability and safety, reduced stress on wheel studs, and improved handling and performance. Hub-centric rings or adapters are used when the wheel’s hub bore is larger than the vehicle’s hub, ensuring proper centering and fitment. When choosing wheels, considering the vehicle’s compatibility, opting for hub-centric aftermarket wheels, and seeking professional installation assistance are crucial factors. Understanding the significance of wheel hub bore helps in making informed decisions and ensuring a smooth and enjoyable driving experience.
Read More: How To Tell Which Wheel Bearing Is Bad?
Focus circle
Wheel bolt patterns are the arrangement and number of bolt holes on a wheel that align with the studs on a vehicle’s hub. Proper fitment of wheels is crucial for safety, stability, aesthetics, and compatibility with brake components and suspension systems.
Ensuring a secure attachment and minimizing the risk of wheel wobbling or detachment while driving is achieved through selecting wheels with the correct bolt pattern. Determining the bolt pattern involves counting the bolt holes and measuring the diameter between opposite holes.
Additionally, considering offset, backspacing, and seeking professional advice when necessary can further ensure proper fitment. Understanding wheel bolt patterns and their significance allows for informed decisions when selecting wheels, resulting in optimal performance and an appealing appearance for your vehicle.
Haul gaps
Haul gaps are the vertical spaces that occur between the axle and the frame of a vehicle when it is loaded or hauling a heavy load. Proper haul gaps are essential for maintaining suspension geometry, load carrying capacity, ground clearance, and ride quality.
Maintaining proper haul gaps helps ensure that suspension components operate within their designed range of motion, prevents overload on the suspension system, maintains ground clearance, and provides a comfortable ride.
Managing haul gaps can be achieved through suspension upgrades, load distribution, suspension adjustments, and regular inspection of suspension components. By effectively managing haul gaps, drivers can ensure safe and reliable performance when carrying heavy loads and preserve the integrity of their vehicle’s suspension system.
Spokes
Spokes are essential components of vehicle wheels that provide structural support, impact resistance, weight reduction, and heat dissipation. They distribute forces, maintain the wheel’s integrity, and enhance overall performance.
Different spoke designs, such as radial, J-shaped, multi-spoke, and split-spoke, offer various strengths, aesthetics, and applications. Radial spokes provide a modern look, while J-shaped spokes offer strength for heavy-duty applications. Multi-spoke designs balance strength, weight reduction, and visual appeal, while split-spoke designs provide a stylish appearance.
Factors to consider when choosing spoke designs include vehicle application, aesthetic preferences, and material selection. By understanding the importance of spokes and considering these factors, drivers can select wheels with optimal spoke designs for improved performance, durability, and visual appeal.
External lip
The external lip of vehicle wheels serves functional purposes such as securing the tire bead, creating an airtight seal, and protecting against curb damage. It plays a vital role in maintaining tire-to-wheel connection, optimal tire pressure, and overall safety.
Additionally, the external lip has a significant aesthetic impact, enhancing the visual appeal of the vehicle and allowing for personalization. It can visually enhance the wheel, alter the perception of wheel size, and be customized to match individual preferences.
When selecting wheels, consider the external lip design that complements the wheel style, suits the vehicle type and purpose, and aligns with personal preferences. Understanding the function and aesthetic impact of the external lip enables car owners to make informed decisions and achieve the desired look and performance for their vehicles.
Barrel
The barrel of a vehicle wheel is a critical component that supports the tire, influences performance, and contributes to the overall aesthetics. It is constructed from durable materials such as aluminum or steel and features a specific profile and thickness.
The design of the barrel impacts the wheel’s weight, rigidity, tire fitment, and visual appeal. Lighter barrels improve handling and fuel efficiency, while stronger designs enhance stability and durability. The barrel’s dimensions determine tire size and shape, affecting performance characteristics.
When choosing a barrel design, consider the vehicle type, style preferences, and performance goals. Understanding the significance of the barrel allows car owners to make informed decisions, ensuring optimal performance and visual enhancement for their vehicles.
Dots
Dots on vehicle wheels serve important functions related to manufacturing, balancing, and tire installation. They act as alignment marks during wheel assembly, ensuring proper positioning of components. Dots can also indicate welding points in wheels with multiple pieces, ensuring secure connections.
Some dots serve as balance indicators, assisting in achieving proper wheel balance by providing reference points for weight placement. They aid in aligning the valve stem and indicating the correct tire orientation during installation.
Understanding the significance of dots provides valuable insights into wheel manufacturing, balancing, and tire mounting processes, enabling car enthusiasts and owners to appreciate the attention to detail involved in these aspects.
HOW WHEELS ARE MADE?
Wheels are typically made using various manufacturing processes, depending on the type of wheel, materials used, and desired characteristics. Here is a general overview of the common methods involved in wheel production:
1. Casting:
- The most common method for manufacturing wheels is casting, which involves pouring molten metal into a mold.
- The mold is typically made of sand or a metal material that can withstand high temperatures.
- The molten metal, usually aluminum or steel, is poured into the mold and allowed to cool and solidify.
- Once cooled, the wheel is removed from the mold and undergoes additional finishing processes.
2. Forging:
- Forging is another method used for wheel production, particularly for high-performance or heavy-duty wheels.
- In this process, a solid piece of metal, usually aluminum or steel, is heated and shaped under high pressure using dies.
- The metal is compressed and molded into the desired wheel shape, resulting in a strong and durable structure.
- After forging, the wheel goes through further machining and finishing processes.
3. Machining:
- Regardless of the initial manufacturing method (casting or forging), wheels often undergo machining processes to refine their shape, dimensions, and surface finish.
- Machining involves using cutting tools, such as lathes and milling machines, to remove excess material and create specific features on the wheel.
- This process ensures precise dimensions, improves balance, and enhances the overall appearance of the wheel.
4. Heat Treatment:
- To enhance the strength and durability of the wheels, heat treatment processes are often employed.
- Heat treatment involves subjecting the wheels to controlled heating and cooling cycles to modify their microstructure and properties.
- This process helps to increase hardness, improve fatigue resistance, and enhance overall performance.
5. Finishing:
- Once the wheels have been cast, forged, machined, and heat treated, they undergo various finishing processes.
- Finishing includes surface treatments like polishing, painting, powder coating, or chrome plating to provide a protective and visually appealing finish.
- These processes can also include applying clear coats to enhance durability and protect against corrosion.
6. Quality Control:
- Throughout the manufacturing process, wheels undergo rigorous quality control inspections to ensure they meet specific standards and requirements.
- Inspections may involve checks for dimensional accuracy, material integrity, surface defects, and overall performance.
- Wheels that pass the quality control checks are ready for distribution and installation on vehicles.
It’s important to note that the specific manufacturing processes and techniques can vary depending on the wheel manufacturer, the intended application (e.g., automotive, motorcycle, bicycle), and the desired wheel design and characteristics.
Throwing
Throwing, in the context of wheel manufacturing, refers to the process of shaping clay on a potter’s wheel to create ceramic objects such as pottery vessels or decorative pieces. While it is not directly related to the production of vehicle wheels, the term “throwing” is commonly associated with pottery making. Here’s a brief explanation of the throwing process:
Preparation:
The potter starts by preparing the clay, ensuring it is at the right consistency and free of impurities. The clay is often wedged or kneaded to remove air bubbles and create a uniform texture.
Centering:
The potter places a lump of clay onto a rotating pottery wheel called a “potter’s wheel” or “throwing wheel.” The wheel spins rapidly, and the potter uses their hands to center the clay mass by applying pressure while keeping it balanced on the wheel.
Opening:
Once the clay is centered, the potter creates an opening in the center of the clay mass using their fingers, thumbs, or specialized tools. This opening will form the interior of the pottery object.
Shaping:
With the initial opening created, the potter begins to shape the clay by pulling, pushing, and manipulating it using their hands, fingers, and various pottery tools. Different techniques, such as pinching, coiling, or using the potter’s wheel, are employed to shape the clay into the desired form.
Thinning and Widening:
The potter continues to refine the shape of the pottery piece by thinning the walls and widening the opening. This is done by gradually applying pressure to the clay with their hands while the wheel spins.
Finishing and Trimming:
Once the desired shape is achieved, the potter may use trimming tools to refine the foot or base of the pottery piece and remove excess clay. They may also add decorative elements or textures at this stage.
Drying and Firing:
After the throwing process, the pottery piece is set aside to dry. Once completely dry, it undergoes firing in a kiln, a process that hardens the clay and transforms it into a ceramic material. The firing process usually involves two stages: bisque firing and glaze firing.
Glazing and Final Firing:
After the bisque firing, the potter may choose to apply glazes or decorative finishes to the pottery piece. The piece is then fired again in a glaze kiln, which melts and fuses the glaze onto the surface, resulting in a glossy or colored finish.
While throwing ceramics on a potter’s wheel is not directly related to wheel manufacturing for vehicles, it is a traditional and artistic process used to create various pottery objects. Vehicle wheels, on the other hand, are typically manufactured using casting, forging, and machining processes, as explained earlier.
Stream Forming
Stream forming, also known as flow forming or flow forging, is a metalworking process used in the manufacturing of cylindrical or tubular components, such as wheels, pipes, and axles. It is a precision forming technique that involves applying controlled pressure to a rotating metal workpiece to reshape and refine its structure. Here’s an explanation of the stream forming process:
Workpiece Preparation:
The process begins with a solid cylindrical or tubular workpiece, usually made of metal, such as aluminum or steel. The workpiece is typically pre-machined or pre-formed to a near-final shape before stream forming.
Setup:
The workpiece is mounted on a lathe or specialized machine designed for stream forming. The machine consists of rollers or forming tools that apply pressure to the workpiece as it rotates.
Rotational Speed and Pressure:
The workpiece is rotated at high speed while pressure is applied to a specific section of the workpiece using the forming tools. The pressure can be applied axially, radially, or both, depending on the desired shape and characteristics of the component.
Metal Flow and Forming:
As pressure is applied, the metal undergoes plastic deformation and starts to flow, redistributing and redistributing material in the desired direction. This controlled flow of metal helps refine the grain structure, improve strength, and enhance the shape of the workpiece.
Dimensional Control:
During the stream forming process, careful control of the applied pressure, rotational speed, and tool movement is essential to achieve precise dimensional control and maintain the desired wall thickness and shape of the component.
Finishing Operations:
After the stream forming process, the formed component may undergo additional machining or finishing operations to refine the final shape, remove any excess material, and achieve the desired surface finish.
Benefits of Stream Forming:
- Enhanced Strength and Durability: Stream forming induces plastic deformation, resulting in grain refinement and improved mechanical properties, such as increased strength and durability of the formed component.
- Dimensional Accuracy: The precise control of pressure and tool movement in stream forming allows for accurate shaping and dimensional control, ensuring consistent and precise components.
- Material Savings: Stream forming can often reduce the material usage compared to other manufacturing processes, as it redistributes and elongates the metal instead of removing excess material through machining.
- Cost Efficiency: Stream forming offers cost advantages in terms of material savings, reduced machining requirements, and improved production efficiency.
- Improved Surface Finish: The process can result in a smooth and polished surface finish on the formed component, reducing the need for additional surface treatments.
Stream forming is a versatile process used in various industries, including automotive, aerospace, and manufacturing, to produce high-quality components with improved mechanical properties and dimensional accuracy. Its ability to enhance strength, achieve precise shaping, and optimize material usage makes it a preferred method for manufacturing cylindrical or tubular components.
Manufacturing
Manufacturing is the process of converting raw materials or components into finished products through various operations, techniques, and technologies. It involves a series of steps that transform the initial materials into a final product suitable for use or consumption. Manufacturing can take place in a wide range of industries, including automotive, electronics, food and beverage, textiles, and more. Here is an overview of the typical stages involved in the manufacturing process:
- Design and Planning: The manufacturing process begins with product design and planning. Engineers, designers, and product developers create detailed specifications, drawings, and prototypes based on market requirements and customer needs.
- Procurement of Raw Materials: Once the design is finalized, the necessary raw materials, such as metals, plastics, fabrics, or chemicals, are sourced from suppliers. Quality and consistency of materials are crucial to ensure the desired product quality.
- Material Preparation: Raw materials often require preparation before they can be used in the manufacturing process. This may involve cutting, shaping, heating, mixing, or treating the materials to achieve the desired properties.
- Manufacturing Operations:
- Forming and Shaping: This step involves transforming the prepared materials into the desired shapes and structures. Processes like casting, molding, forging, extrusion, or machining are employed to shape the materials.
- Assembly: In assembly operations, individual components are brought together and connected to form the final product. Assembly techniques can include manual or automated processes, such as welding, fastening, soldering, or adhesion.
- Finishing: Once the product is assembled, various finishing operations are performed to improve its appearance, functionality, and durability. This may include processes like painting, coating, polishing, engraving, or surface treatment.
- Quality Control: Throughout the manufacturing process, quality control measures are implemented to ensure that the product meets specified standards and requirements. Inspections, testing, and quality assurance procedures are conducted to identify and address any defects or deviations.
- Packaging and Logistics: Once the manufacturing process is complete, the finished products are packaged, labeled, and prepared for shipping or distribution. Packaging serves to protect the product during transportation and provides essential information to the end-user.
- Distribution and Sales: Finished products are then distributed to retailers, wholesalers, or directly to customers. The products may be sold through various channels, including brick-and-mortar stores, online platforms, or specialized distributors.
- After-Sales Support: After-sales support involves activities such as product maintenance, warranty services, repairs, or customer support to address any issues or inquiries from consumers.
Manufacturing processes can vary significantly depending on the industry, product complexity, and production volume. Advanced technologies like automation, robotics, and computer-aided systems are increasingly utilized to improve efficiency, precision, and productivity in manufacturing operations. Continuous improvement efforts and lean manufacturing principles are also employed to optimize processes, reduce waste, and enhance overall product quality.
Revolving Forging
This procedure was spearheaded by TSW Wheels and is being utilized by Motegi Racing Wheelsas well. It is like standard aluminum producing however with a wind.
While the billet is being fashioned, the manufacture is turning at high speeds. This powers the particles to frame solid chains.
This structure results in a wheel that is more grounded than a customarily fashioned aluminum wheel.
WHEEL SIZES
Wheels arrive in a wide scope of sizes. The low-end is secured by 15 inch wheels; monstrous 26 inch wheels command the upper end and wheels of all sizes are accessible in the middle.
Things being what they are, if your vehicle or truck comes stock with 16 inch wheels for what reason would you need another size? Two reasons: tasteful intrigue and execution.
Bigger wheels simply look better. They round out the wheel well and that gives visual effect. It’s what we call unadulterated wheel sight to behold. Bigger wheels convey tires with littler sidewalls so you show signs of improvement hold and execution.
For rough terrain vehicles, this means less roll and influence and greater solidness.
The main drawbacks to upsizing are that bigger haggles gauge all the more so gas mileage experiences and speeding up 0 to 60 is debased.
Vehicle and Driver examines additionally discovered that at as far as possible, the suspension is burdened and the ride can endure.
Remember, your vehicle was initially designed to move on stock size wheels.
That implies the speedometer, odometer, footing control, torque and outfitting settings depended on the separation that the stock haggle get together would cover in one transformation.
When you change the span of the wheel you should keep up the general distance across of the haggle gathering.
Along these lines, as your wheels get bigger, the standing size of the tire gets littler.
A decent principle guideline is that for each expanded inch of wheel breadth you should diminish an inch of standing tallness. This keeps up the general measurement.
That implies the haggle will in any case spread a similar measure of separation in one pivot yet it will look so much better doing as such.
A wheel estimate is communicated as pursues:
DxW
Where D = breadth and W = width.
For instance: 18×9 methods the breadth of the wheel is 18 inches and the width is 9 inches.
- 15×10 wheels
- 17×9 wheels
- 20×10 wheels
- 20×12 wheels
- 20×14 wheels
- 22×12 wheels
- 22×14 wheels
Jolt PATTERNS
The jolt design is comprised of the quantity of jolts and the distance across of the fanciful circle they make (BCD). The BCD can be communicated in inches or millimeters.
Jolt designs with a much number of jolts are estimated from jolt focus to jolt focus. 5 carry jolt designs are estimated from the focal point of the upper jolt to the base of the lower jolts.
A jolt design is communicated as pursues:
NxBCD
Where N = number of jolts and BCD = jolt focus distance across.
For instance, in the event that you have a 5 carry haggle jolt focus estimates 114.3 millimeters then your jolt design is 5×114.3.
Here are instances of regular jolt designs. Each connection gives you a chance to peruse existing wheels with that jolt design:
- 4×100 wheels
- 4×114.3 wheels
- 5×100 wheels
- 5×112 wheels
- 5×114.3 wheels
- 5×120 wheels
WHEEL OFFSET
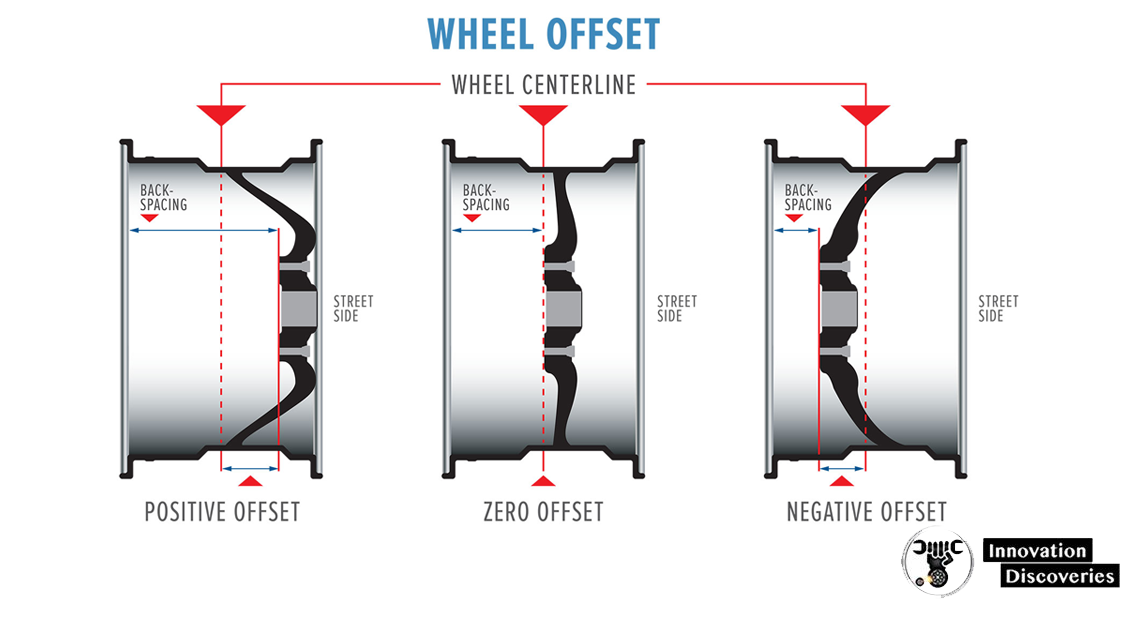
Wheel offset refers to the distance between the wheel’s mounting surface and the centerline of the wheel. It is an essential measurement when fitting wheels onto a vehicle and plays a significant role in determining the wheel’s positioning within the wheel well.
Positive Offset:
When the mounting surface of the wheel is closer to the outside (front) of the wheel, it is referred to as a positive offset. This means that the wheel sits more inward towards the vehicle’s suspension components. Positive offset wheels are commonly found in most vehicles and provide better clearance for suspension parts, ensuring proper fitment and minimizing the risk of interference.
Negative Offset:
When the mounting surface of the wheel is closer to the inside (back) of the wheel, it is considered a negative offset. Negative offset wheels protrude further out from the wheel well towards the fender. They can provide a more aggressive or “deep-dish” look, but they may require additional modifications, such as fender rolling or trimming, to prevent rubbing against suspension components or the fender itself.
Zero Offset:
A zero offset means that the mounting surface of the wheel is positioned exactly at the centerline of the wheel. This results in equal spacing on both the inner and outer sides of the wheel. Zero offset wheels are commonly used in applications where a specific offset is not required or when accommodating aftermarket brake systems that require a specific clearance.
Wheel offset is typically measured in millimeters (mm) and is often stamped or engraved on the wheel itself. It is crucial to select the appropriate offset when replacing or upgrading wheels to ensure proper fitment, adequate clearance for suspension and brake components, and to maintain optimal handling characteristics. Vehicle manufacturers provide recommended offset ranges for specific models, and exceeding these limits may lead to fitment issues or compromised performance.
Additionally, modifying the wheel offset may have an impact on the vehicle’s overall track width, which can affect handling, stability, and tire wear patterns. It is advisable to consult with a knowledgeable professional or refer to manufacturer guidelines when selecting wheels with the correct offset for your vehicle.
One Piece Wheels Versus Two Piece Wheels
There are two sorts of wheels: one-piece haggles piece or Two-piece wheels.
One-Piece Wheels:
One-piece wheels, as the name suggests, are wheels that are manufactured as a single unit, with the center hub, spokes, and rim all formed as one piece. They are commonly made from materials such as aluminum alloy or steel. Here are some key characteristics of one-piece wheels:
- Construction: One-piece wheels are cast or forged in a single piece, resulting in a solid and continuous structure.
- Design Options: They offer a wide range of design options, including various spoke patterns, finishes, and sizes, allowing for customization to suit different styles and vehicle applications.
- Weight: One-piece wheels tend to be lighter compared to two-piece wheels due to their simpler construction. Lighter wheels can provide benefits such as improved acceleration, handling, and fuel efficiency.
- Cost: One-piece wheels are generally more cost-effective compared to two-piece or multi-piece wheels. The manufacturing process is relatively simpler, leading to lower production costs.
Two-Piece Wheels:
Two-piece wheels are composed of two separate components: the center hub and the outer barrel. The center hub typically consists of the spokes and the mounting surface, while the outer barrel forms the outer edge of the wheel. Here are some characteristics of two-piece wheels:
- Construction: Two-piece wheels involve the joining of the center hub and the outer barrel, typically through welding or bolts. This construction method allows for flexibility in design and customization.
- Fitment Options: Two-piece wheels often offer a broader range of fitment options, including different widths and offsets, allowing for more precise fitment on various vehicles.
- Styling Options: The two-piece construction allows for unique styling elements, such as exposed hardware or customizable color combinations between the center hub and the outer barrel.
- Weight: Two-piece wheels can vary in weight depending on the specific components and materials used. They may be lighter or heavier than one-piece wheels, depending on the design and materials chosen.
- Cost: Two-piece wheels generally tend to be more expensive than one-piece wheels due to the additional manufacturing processes involved, such as joining the components and the potential for customization.
Both one-piece and two-piece wheels have their advantages and considerations, and the choice between them often depends on personal preferences, budget, intended use, and the specific aesthetic and performance requirements of the vehicle. It’s important to consider factors such as weight, design options, fitment, and cost when selecting the appropriate wheel type for your needs.
Read More: